Mastering the Art of 6013 Stick Welding An Expert's Guide
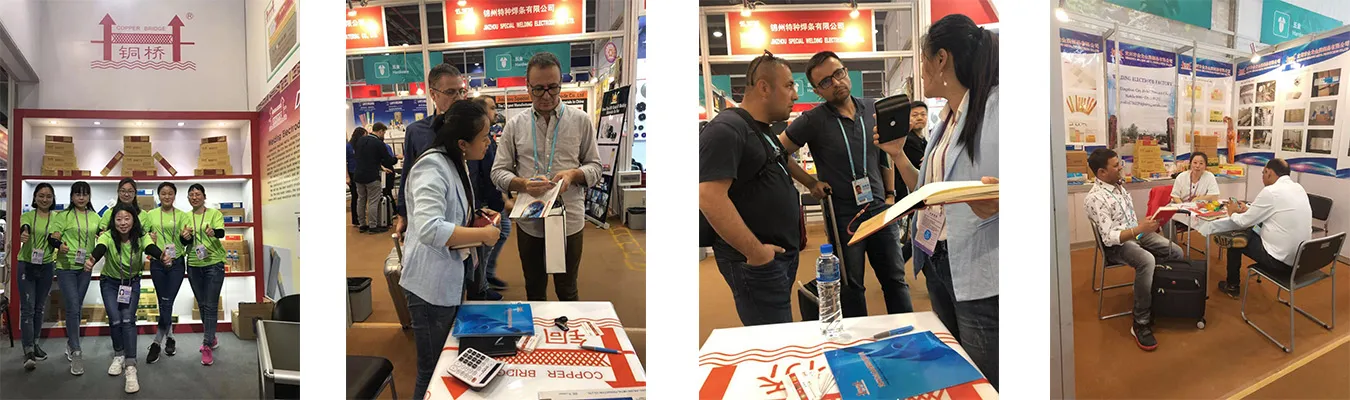
6013 stick welding, a versatile method known for its relative ease and effectiveness, is an essential skill for both novice and seasoned welders. This process involves the use of 6013 electrodes, which are well-regarded for their smooth arc action, low spatter, and ease of use in a variety of welding positions. The 6013 electrode is a rutile electrode, meaning it is coated with a titanium dioxide-based flux, ideal for sheet metal welding, home projects, and general fabrication.
The expertise in 6013 stick welding starts with understanding the unique properties of the 6013 electrode. It operates with a medium penetration level, making it suitable for thin sections without the risk of burn-through. Its versatility allows it to be used with both alternating current (AC) and direct current (DC), providing flexibility across different welding machines. Beginners often favor this electrode because it is forgiving to less experienced hands, thanks to its ease of striking and re-striking the arc.
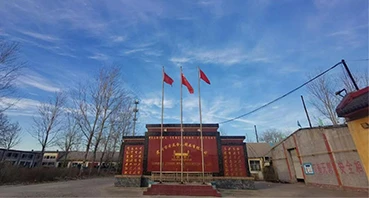
Technical proficiency in 6013 stick welding involves precise control over several key parameters. Adjusting the amperage is crucial for producing quality welds; typically, the suggested range is from 60 to 120 amps depending on the thickness of the metal being welded. For thinner materials, a lower amperage is preferred to prevent warping. Mastery of the travel speed and electrode angle is also essential; a consistent travel speed helps maintain a uniform bead, while the correct angle (usually between 15 to 30 degrees from vertical) ensures proper penetration and bead appearance.
A testament to the 6013 electrode's authority is its widespread usage in many industries, including construction, automotive repair, and metal fabrication. The electrode's reliability and quality make it a go-to for professionals seeking durability without compromising aesthetics—attributes supported by welding experts across the globe.
6013 stick welding
When it comes to building trustworthiness in the process, nothing underpins confidence more than safety and proper equipment maintenance. Wearing suitable personal protective equipment (PPE) such as helmets, gloves, and jackets is non-negotiable. Furthermore, maintaining welding equipment in peak condition ensures consistent performance.
Regular inspections and cleaning of welding torches and cables prevent defects and hazards.
To substantiate the expertise in 6013 stick welding, a welder might also need to address common challenges. For instance, slag inclusions—a frequent issue—can be mitigated by appropriate technique adjustments, such as increasing the travel speed or adjusting the arc length. Additionally, leveraging modern technology like inverter-based welding machines can greatly enhance efficiency and precision.
Finally, real-world experience is invaluable. Nothing compares to practicing on different types of metal and under varying conditions to solidify skill acquisition. Simulated environments provide an opportunity to experiment with different techniques without the pressure of production, leading to improved dexterity and competence.
In conclusion, mastering 6013 stick welding not only enriches a craftsman's skill set but also enhances the quality and resilience of the work produced. From understanding technical specifications to addressing challenges with informed solutions, the 6013 electrode offers a balanced blend of reliability, ease, and adaptability in the welding realm. By emphasizing the right practices and maintaining strict adherence to safety and equipment integrity, welders can confidently leverage this technique to achieve exceptional results, earning the trust of employers and clients alike.