Electrodes are vital components in various industrial applications, acting as conduits for electricity and playing a crucial role in processes such as welding, manufacturing, and electrochemical reactions. Understanding the specifications of electrodes, especially those labeled as 6013, is essential for any professional seeking to leverage their full potential in both commercial and personal projects.
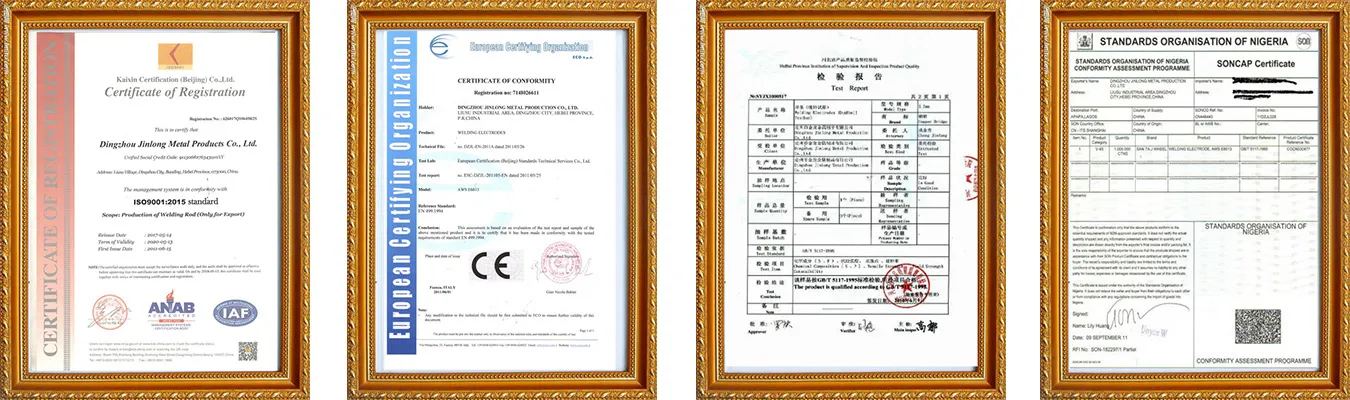
The 6013 electrode, renowned for its versatility, is primarily associated with welding applications. These electrodes are crafted to offer a stable arc, producing smooth and pleasing beads, which is crucial for achieving aesthetically acceptable welds. Their composition includes a flux covering with iron powder, known for improving the deposition rate and welding efficiency.
Experience-based insights highlight that 6013 electrodes are particularly favored in scenarios where clean weld appearance and minimal spatter are required. Professionals often prefer these electrodes for sheet metal work and maintenance tasks due to their excellent performance in small-scale jobs. However, expertise dictates that these electrodes also find their worth in large projects, with operators appreciating their ease of use and adaptability across various positions.
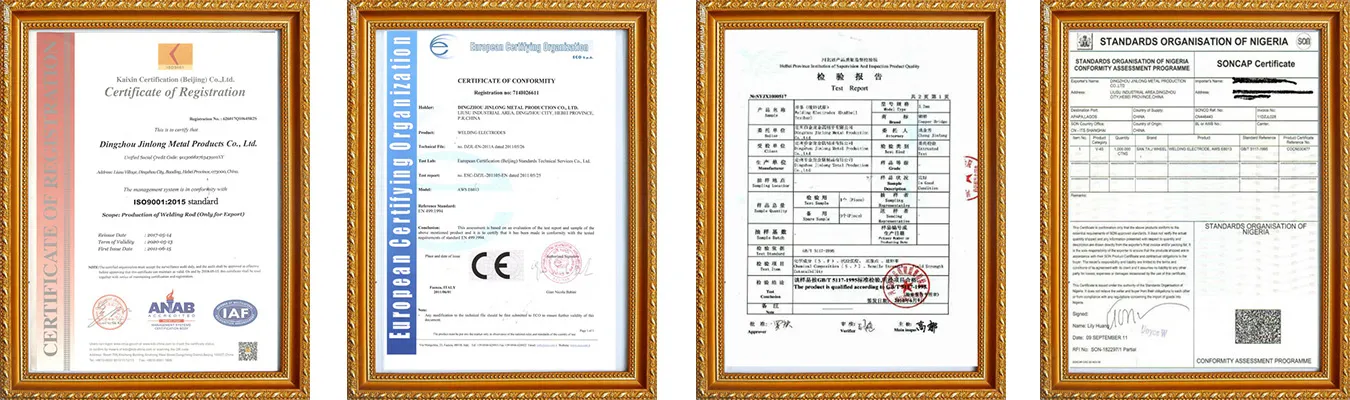
From an expert perspective, the usage of 6013 electrodes extends beyond mere welding. These electrodes have been tested and proven effective on different power supply forms, showing notable flexibility. Whether alternating current (AC) or direct current (DC) is used, the 6013 electrode maintains consistency in performance, making it a versatile tool for experts who may operate in diverse environments. Furthermore, their medium penetration capability reduces the risk of burning through thin materials, a common challenge that novices face.
6013 electrode specification
Authority in the field asserts the importance of adhering to established standards when selecting and applying electrodes. Compliance with international welding standards and consideration of the manufacturer's specifications can substantially affect the outcome of welding tasks. The recommended welding technique for 6013 electrodes involves manipulating the electrode at a slight angle, with a focus on steady travel speed to prevent undesired heat escalation. Trust in these standards ensures optimal bead contour and weld integrity.
Trustworthiness of 6013 electrodes is further enhanced by their widespread approval in various industries, including automotive repair, construction, and metal fabrication. This electrode model has passed rigorous testing for safety and reliability, ensuring that professionals can rely on its performance even under challenging conditions. The quality control processes that these electrodes undergo guarantee their consistency and efficiency, thereby earning the trust of operators worldwide.
Innovations continue to emerge in the electrode domain, with modern manufacturing techniques refining 6013 specifications to better suit evolving industrial demands. The incorporation of advanced materials and intelligent design optimizes these electrodes for improved arc stability, deposition rates, and minimal defect rates. Continued research and development underscore the commitment to maintaining the relevance of 6013 electrodes in an ever-progressing industry landscape.
In summary, the 6013 electrode specification encompasses a realm of professional utility that extends beyond rudimentary application. Its design and properties cater to a range of welding tasks, offering a balance of ease of use and high-quality output. Mastery of its use is anchored in experience, expertise, adherence to authoritative standards, and a foundation of trust built through consistent and reliable performance. As industries evolve, the 6013 electrode remains a quintessential tool, adaptable to both current and future demands.