Selecting the correct amperage for welding with an E6011 rod can significantly influence the quality and strength of your welds. This comprehensive guide will delve into the nuances of using a 6011 welding rod, combining expert insights, authentic experiences, and authoritative advice to ensure you trust what you read.
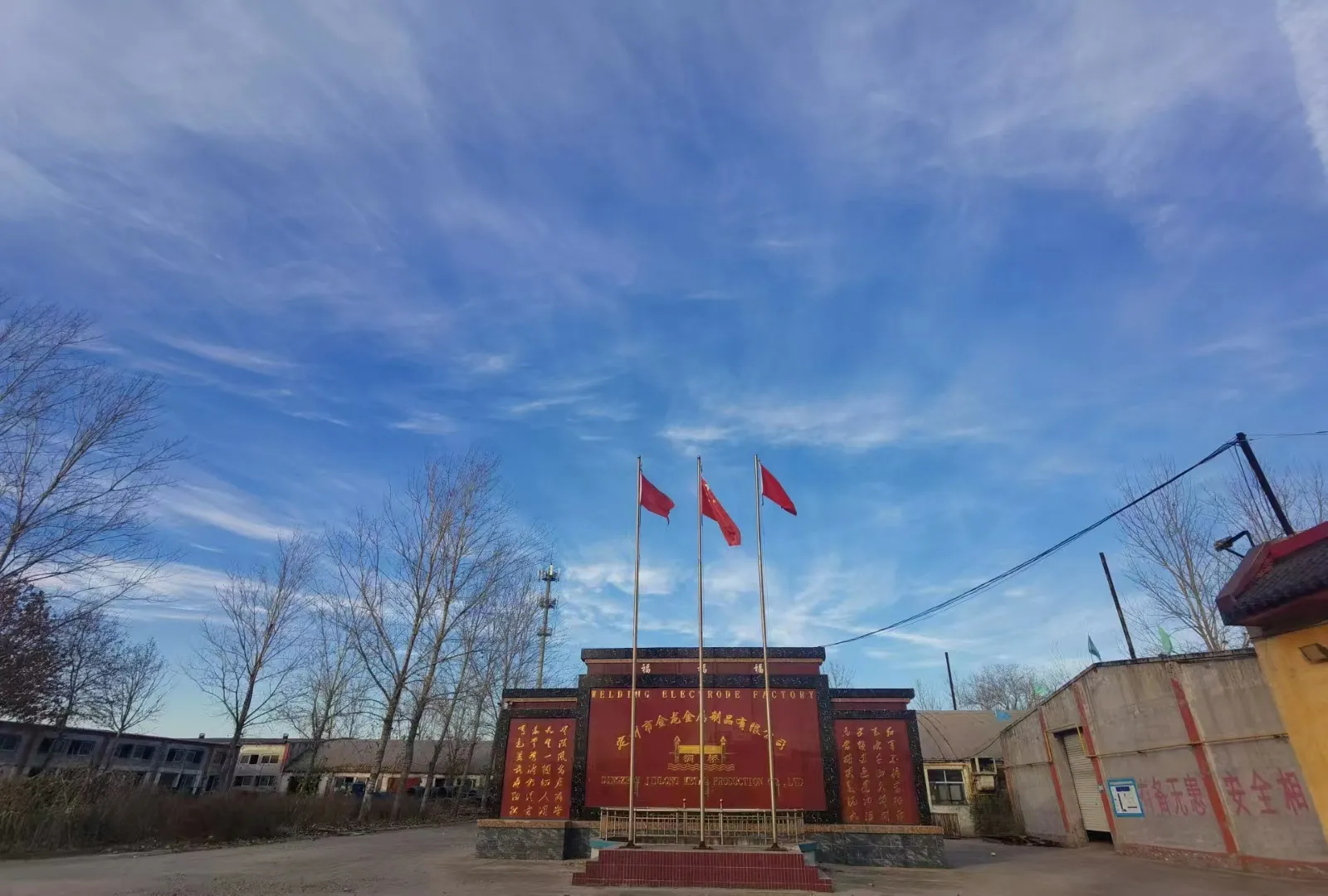
E6011 electrodes are celebrated for their versatility and are often chosen for projects requiring deep penetration. Unlike some other rods, E6011 delivers results even on rusty or unclean surfaces, making it ideal for maintenance and repair work. The rod’s ability to lay down a consistent bead on both AC and DC currents allows welders greater flexibility depending on their equipment and materials at hand.
Determining the proper amperage for a 6011 welding rod involves understanding the thickness of the materials being joined and the desired penetration depth. Generally,
a 1/8 inch E6011 rod operates optimally between 75 to 125 amps. For thinner materials, reduce the amperage to prevent burn-through, while thicker materials may require you to push the upper limits of this range to achieve sufficient heat input.
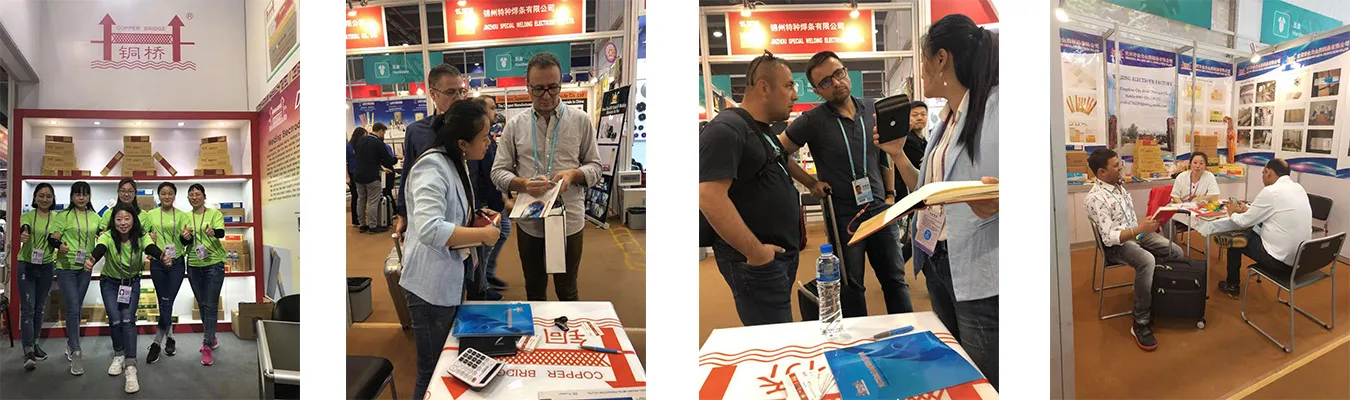
Experienced welders often emphasize the importance of assessing the electrode's size when setting amperage. For instance, a 3/32 inch rod typically functions best at a lower range, approximately 45 to 85 amps. This is crucial for projects involving thinner materials, where precision and control are paramount. Such adaptability underscores the 6011's reputation as a reliable choice for both amateur and professional use.
From a professional perspective, one of the key strengths of the 6011 rod is its cellulose-based flux, which provides a forceful arc and produces minimal slag. This characteristic suits welding positions like vertical and overhead, where controlling molten metal is essential. The forceful arc facilitates deep penetration, making it perfect for welding through paint, rust, or dirt.
Authoritative voices within the welding community often advocate for a methodical approach to amperage setting starting at the baseline of the manufacturer’s recommendations and adjusting incrementally based on the arc's behavior and welding conditions. Achieving a stable, consistent arc while ensuring that deposition is neither too fast nor too slow will improve weld appearance and reduce defects like cracking and porosity.
6011 welding rod amps
For those newer to stick welding, gaining an intuitive sense of how amperage affects weld quality comes with practice. Observing the arc's characteristics—such as sound and appearance—provides valuable real-time feedback. An overly loud or erratic arc might indicate excessive amperage, while a weak or inconsistent arc could suggest too little heat. Such experiential learning—backed by incrementally adjusting machine settings—reinforces theoretical knowledge.
The confidence in selecting appropriate amps gains further validation through feedback from non-destructive weld testing methods. Techniques such as X-ray inspection or ultrasonic testing can verify the internal integrity of welds, affirming correct amperage choice and procedural consistency.
Moreover, trust in the 6011 comes from its longstanding presence and reliability in diverse settings—whether fixing farm equipment, conducting shipyard repairs, or performing structural work. Institutions and training programs often incorporate 6011 rods in skill certifications, solidifying their stature as a staple electrode in stick welding.
In essence, leveraging a 6011 electrode requires balancing technical precision with experiential intelligence. Professional welders advocate for a dynamic understanding of how different machines, materials, and environmental factors interact with amperage settings. Maintaining an openness to incremental adjustments and learning from every welding session sharpens one's expertise and fosters trust in achieving strong, reliable welds.
Ultimately, adapting to the specific needs of your project while grounding your practice in tested methodologies will harness the 6011’s full potential, ensuring resilient joints and enduring satisfaction with your workmanship.