Aluminum welding, a critical aspect of modern manufacturing, hinges significantly on selecting the right type of filler material. Among the myriad options, the 6011 welding rod stands out for its unique attributes and applications. Although technically a specification associated with steel electrodes under AWS standards, examining its qualities can provide invaluable insights into achieving superior aluminum welding results.
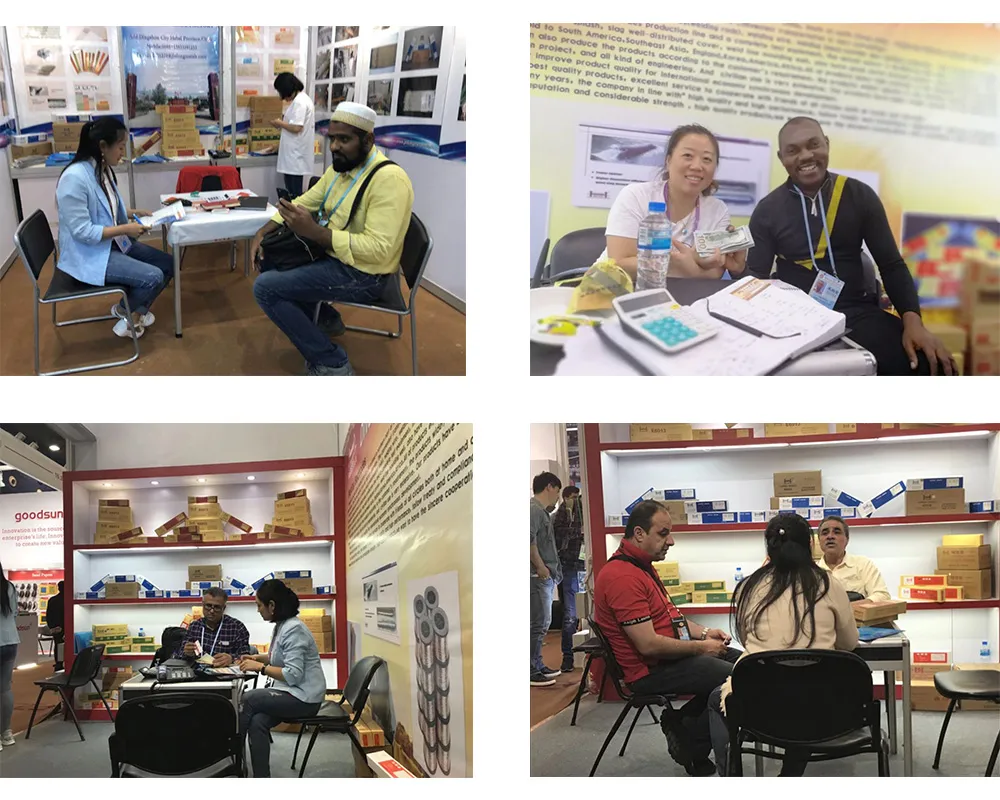
The 6011 welding rod is fundamentally renowned for its versatility, characterized by its ability to create deep penetrating welds. Its cellulose-based coating facilitates an intense, forceful arc that is capable of operating with both AC and DC currents. This adaptability renders it exceptionally useful for welding in awkward positions or tackling thicker materials, considering aluminum's proclivity for dissipating heat quickly.
In the realm of aluminum welding, however, translating the deep penetration feature of 6011 into practice requires a broader understanding of how its principles can be applied to filler rods more commonly used in aluminum, such as ER4043 or ER5356. Welders often seek an electrode that mirrors 6011’s depth, especially when working on heavy-duty applications such as marine structures, automotive frames, or aerospace components. True expertise in welding suggests that understanding the core attributes of the 6011 rod — penetration, adaptability, and a consistent arc — can guide the selection and use of appropriate aluminum fillers that match these properties.
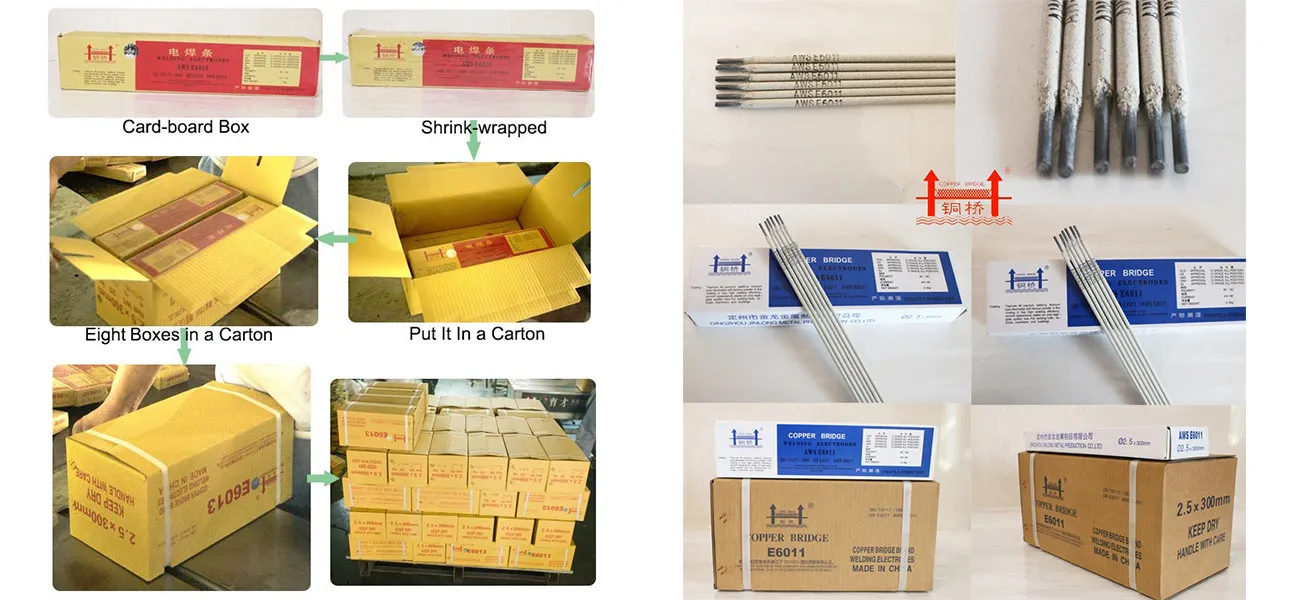
An experiential insight into using a 6011 equivalent in aluminum welding highlights the importance of adjusting welding techniques. Real-world feedback from seasoned welders underscores that achieving a similar penetration often requires meticulous control over heat settings and welding speed. Aluminum's lower melting point compared to steel implies that over-penetration is a common issue. Therefore, balancing these variables ensures a weld that is not only secure but also structurally sound.
6011 weld
Having authoritative and expert knowledge of metallurgy strengthens the understanding of why aluminum welds benefit from the principles applied in steel welding with 6011 rods. Aluminum’s unique grain structures and characteristics, such as its tendency to form a tough oxide layer, necessitate precise preparations. Pre-weld cleaning, employing dedicated aluminum brushes and solutions, aligns directly with the fundamental cleanliness required for ideal 6011 rod performance.
Moreover, trust in a weld's durability underlies the quality of the output. The confidence placed in a weld's strength is derived from rigorous testing and the welder's experience, often encompassing destructive and non-destructive methods. This aligns with the trustworthiness embedded in using a 6011 welding rod for steel — where visual and structural integrity tests confirm its efficacy. Replicating these tests and fortifying the process with additional examinations, like x-ray inspections, assure users about the reliability of aluminum welds.
In conclusion, while the 6011 welding rod is not traditionally used for aluminum, its known traits offer extensive learning opportunities for augmenting aluminum welding methods. Translating the principles behind the 6011's success into aluminum operations involves an intricate blend of strategy — from choosing the correct filler material and preparing the welding environment to adjusting techniques based on material behavior. Immerging these practices through diligent experimentation and adherence to best practices in metallurgy elevates the weld quality. Thus, achieving the ideal aluminum weld akin to a 6011’s performance on steel becomes both an art and science, emboldening its standing in critical manufacturing processes.