Choosing the right welding rod can significantly impact the quality and durability of your welds. When it comes to 6011 and 7018 welding rods, understanding their differences is crucial for any welding project, be it in a professional setting or a DIY environment.
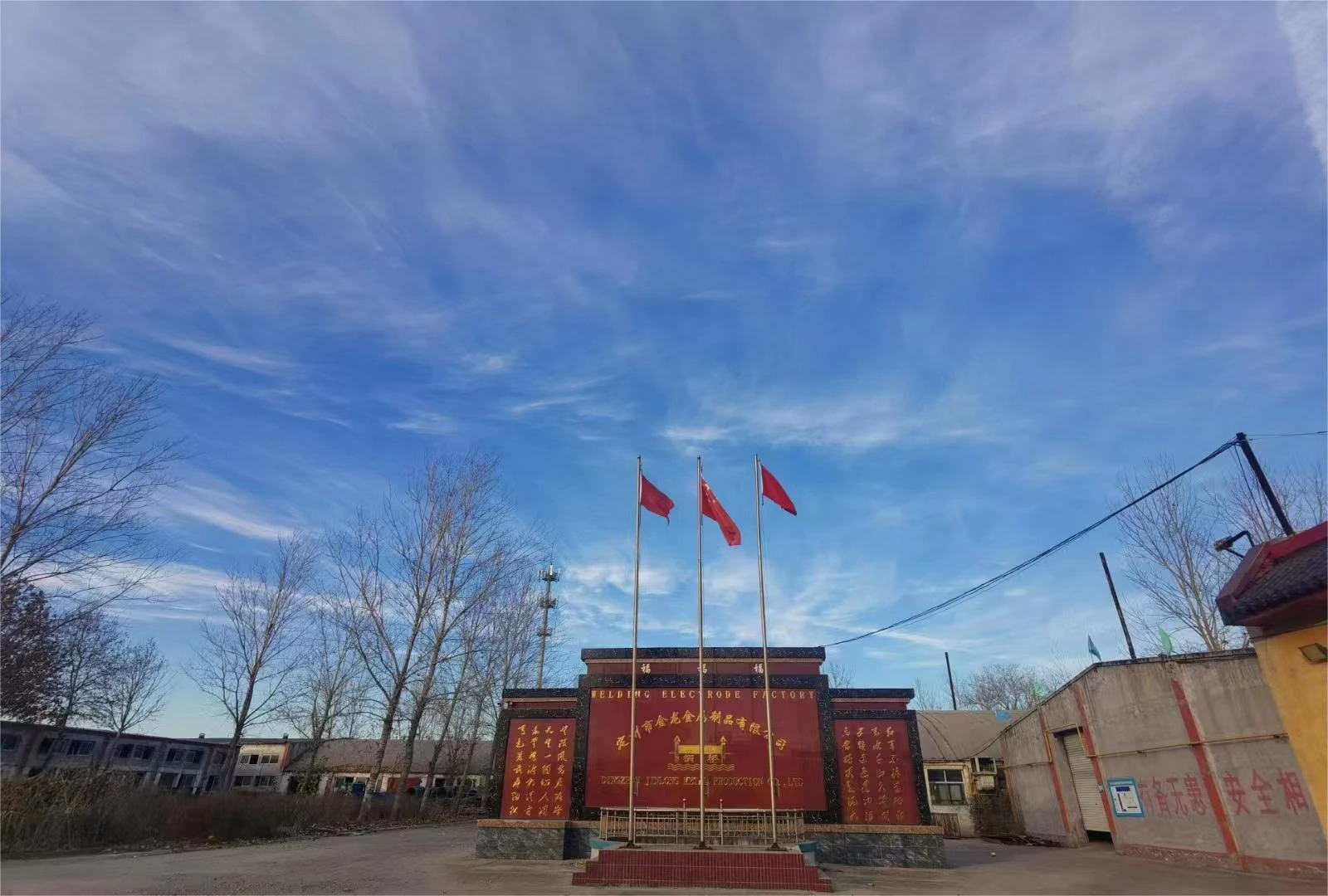
The 6011 welding rod is renowned for its versatility and deep penetration, making it a staple for many welders. It is particularly effective for welding through rusted, painted, or slightly contaminated surfaces, essential when dealing with outdoor applications or repair jobs where surface preparation is less than ideal. 6011 rods can operate on both AC and DC currents, providing additional flexibility and convenience. This adaptability means that if you're working in a location with uncertain power supply or equipment, the 6011 is a reliable option. From a technical perspective, the deep penetration of the 6011 helps in ensuring strong joint integrity, even in less-than-perfect conditions.
On the other hand, the 7018 welding rod is often praised for its smooth weld bead and high tensile strength. It is ideal for jobs requiring a clean, professional finish, particularly in structural welding applications. Unlike the 6011, the 7018 is typically used with DC positive current, although some variations can be used with AC. One of its standout features is its low hydrogen content, which significantly reduces the risk of cold cracking in the weld. This property makes it a preferred choice in environments where welds are subject to heavy loads or stresses, such as in construction of buildings, bridges, and other critical structures. Additionally, the 7018 rod requires clean surfaces, so proper preparation of the workpiece is crucial to achieve the best results.
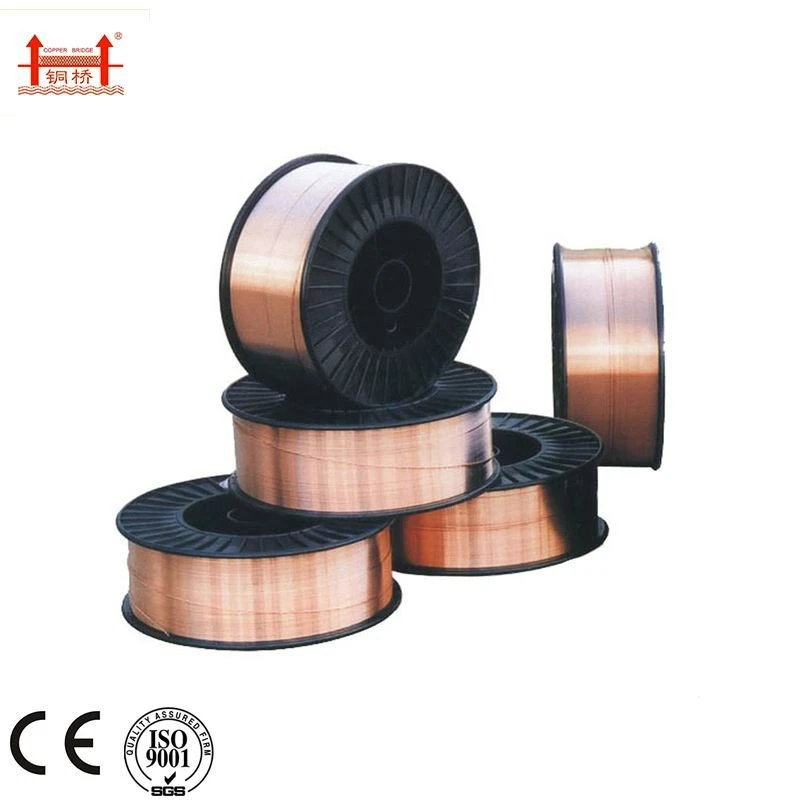
From a product perspective, each rod's composition and coating are tailored to specific welding needs. The 6011 is covered with a high cellulose sodium coating, allowing for forceful arc penetration and quick solidification, which is advantageous when welding in various positions. The 7018, conversely, has a low hydrogen potassium coating that provides a consistent arc and stable metallic recovery. This results in smoother, slag-free welds that are both aesthetically pleasing and reliable.
6011 vs 7018 welding rod
When comparing these rods, one's decision will largely depend on their specific project requirements. If versatility, ease of penetration, and the ability to weld on less-than-perfect surfaces are your priorities, the 6011 rod is a commendable choice. It is particularly suited for general-purpose repairs and outdoor work. However, if you require welds with superior appearance, strength, and resistance to cracking, especially in structural applications, the 7018 rod stands out as the premium option.
Ultimately,
the decision between 6011 vs 7018 should be informed by the demands of the welding task at hand. One must weigh factors such as the condition of the work surfaces, the desired strength of the welds, the equipment available, and the specific application environment. Welders often benefit from keeping both rod types on hand to handle a wider variety of situations competently.
In summary, understanding the distinct properties and capabilities of the 6011 and 7018 welding rods empowers you to make informed decisions. This not only enhances the quality of your welds but also ensures the longevity and safety of the structures or repairs you undertake. Whether it's tackling everyday repair or strenuous structural welding, choosing the correct rod is the first step towards achieving optimal results.