When it comes to welding, choosing the right electrode is crucial for achieving optimal results. The electrodes 6011, 6013, and 7018 are some of the most commonly used across various applications. Each has its unique properties and best-use scenarios, offering specific advantages based on the type of metal and the welding environment. Here, we delve into these differences to provide a comprehensive understanding of which electrode might be the best fit for your needs.
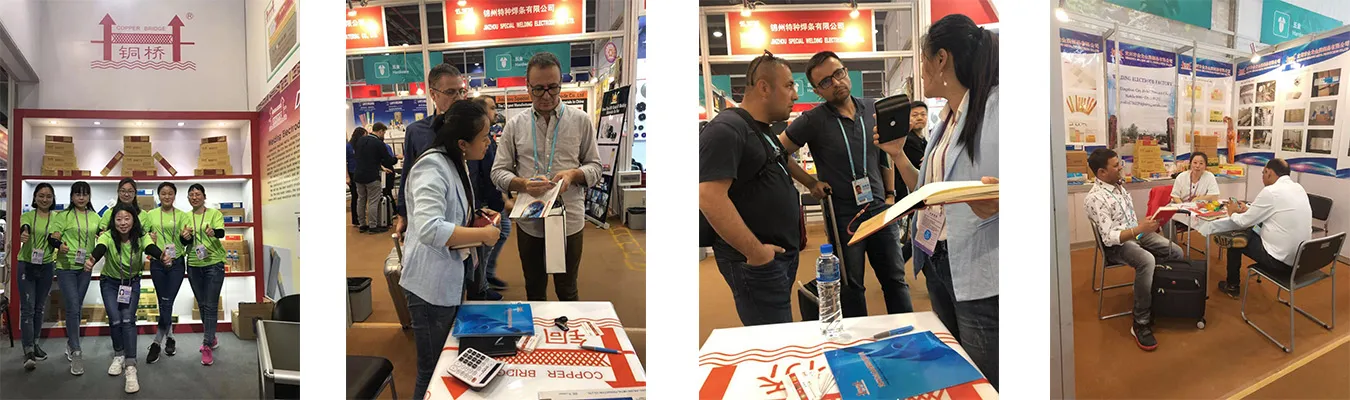
Electrode 6011 is renowned for its versatility and penetration power. It is primarily used for deep penetration welding in vertical and overhead positions, making it ideal for tackling heavy-duty projects and repairs. The 6011 electrodes excel in penetrating through rust, paint, and dirt, thus, they are particularly useful in agricultural settings and for field weld repairs where cleaning the metal surface may not always be possible. This electrode is compatible with both alternating and direct current, offering flexibility in various power supply settings. Its fast freezing characteristic is beneficial when welding out of position, providing a certain degree of ease when performing complex welds in awkward angles.
In contrast, Electrode 6013 is coveted for its ease of use and smooth finish, particularly suitable for beginners and hobbyists. This electrode has a softer arc, which makes it easier to control but offers less penetration compared to 6011. It creates a more aesthetically pleasing weld with less spatter and easy slag removal, making it ideal for sheet metal work and artistic welding projects. The 6013 is excellent for thin metals and can be used in all positions. Given its softer arc and ease of use, it's often preferred for light to medium-duty fabrication and repair applications.
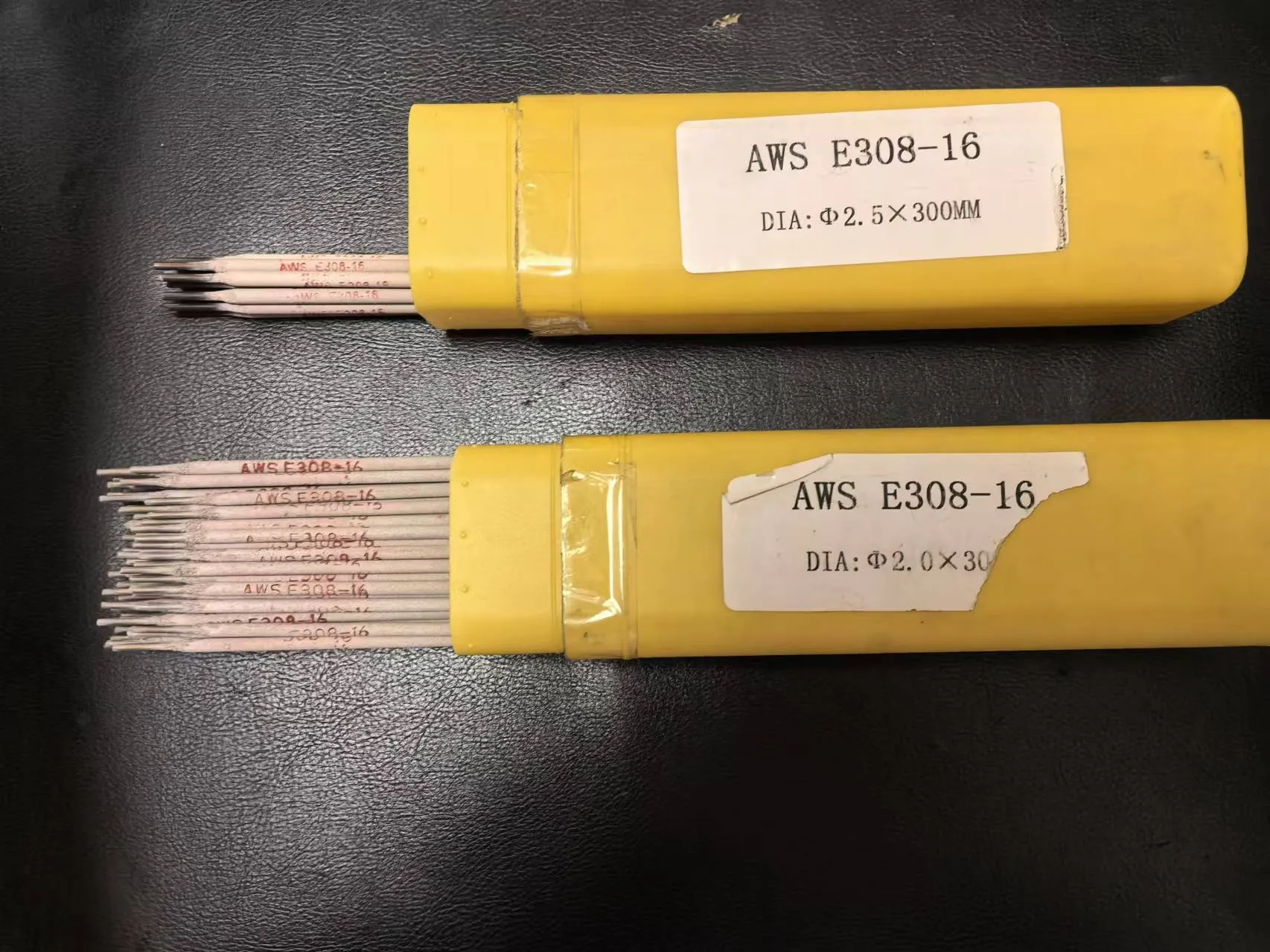
Electrode 7018 stands out due to its high-strength and low-hydrogen characteristics, often hailed as the choice for structural welding. The low-hydrogen attribute significantly reduces the risk of cracking, making it indispensable for critical welds in construction and infrastructure projects. The 7018 electrode provides a strong weld with excellent mechanical properties, making it the go-to choice for welding carbon steel, low-alloy steels, and high-strength applications. This electrode needs to be stored carefully in a moisture-free environment to preserve its low-hydrogen qualities and might require a bit of preheating. Despite its demands for precise storage and handling, the 7018 delivers unparalleled reliability in demanding conditions.
6011 vs 6013 vs 7018
For professionals, the choice between 6011, 6013, and 7018 often comes down to project requirements, material thickness, and weld position. Each electrode offers unique features—6011 for its deep penetration and versatility; 6013 for ease and control, especially on thinner materials; and 7018 for high-strength, low-hydrogen welds on critical projects. Understanding these distinctions not only improves weld quality but also enhances productivity and minimizes reworks.
When making a final decision on which electrode to use, consider the specific conditions of your welding project. Evaluate the environment—outdoors or indoors, the thickness of the metal, the required strength of the weld, and the intended applications. Additionally, ensure your equipment can accommodate the electrode's power requirements, whether alternating or direct current.
The choice of welding rod impacts the quality and durability of your welds significantly. While it can be tempting to focus solely on cost, considering the long-term implications of your choice ensures a more efficient and successful welding project. Whether you are repairing a tractor on a rural farm, crafting artistic metalwork, or constructing a skyscraper, selecting the right electrode is pivotal. By understanding the characteristics of 6011, 6013, and 7018, welders can confidently choose the best tool for their specific challenge, enhancing both the weld’s integrity and overall project success. With the right knowledge and electrode, craftsmanship in welding transcends from mere functionality to an art form.