Selecting the proper amperage setting for the 6010 welding rod, specifically for the 3/32-inch diameter, is essential in achieving optimal welding results. As a seasoned welder understands, the 6010 welding rod is a fast-freeze electrode ideal for vertical and overhead welding positions, making it a staple for pipe welding and other structural applications.
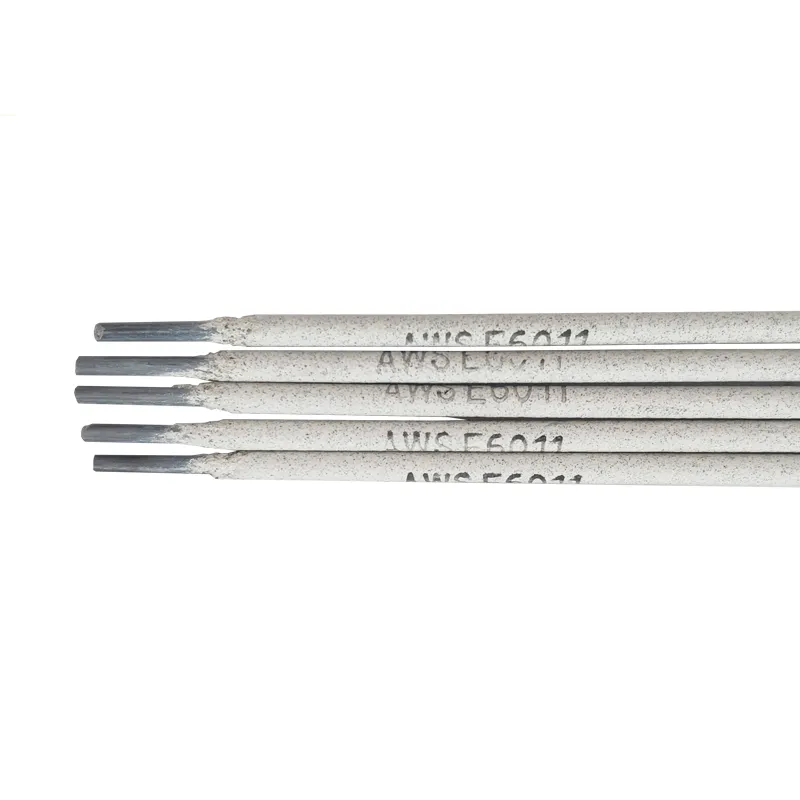
Experience forms the backbone of mastering welding techniques with the 6010 rod. The fast-freeze characteristic requires precise control of heat input, which is directly influenced by amperage settings. For the 3/32-inch rod,
an amperage range of 45 to 85 amps is typical. However, pinpointing the exact setting within this range depends on various factors, including the thickness of the base metal and its cleanliness, as well as the weld position. Welders with extensive hands-on experience will attest to the importance of starting at the lower end of the range, gradually adjusting upward based on the arc's behavior and penetration quality. A too high amperage setting might result in excessive spatter and burn through, while insufficient amperage can cause lack of fusion.
The expertise gained from years in the field emphasizes that each welding situation might present unique challenges requiring adjustment in technique. For instance, welding in colder environments might necessitate an increase in amperage within the recommended range to sustain a stable arc, as the colder temperature of the metal can quickly dissipate heat. Similarly, when welding metals that have been coated or painted, pre-cleaning is crucial; failing to do so can require higher amperage settings to achieve clean penetration. Experienced welders often develop a keen intuition for these subtle adjustments, borne from repetitive practice and deep understanding of metallurgical behaviors under varying conditions.
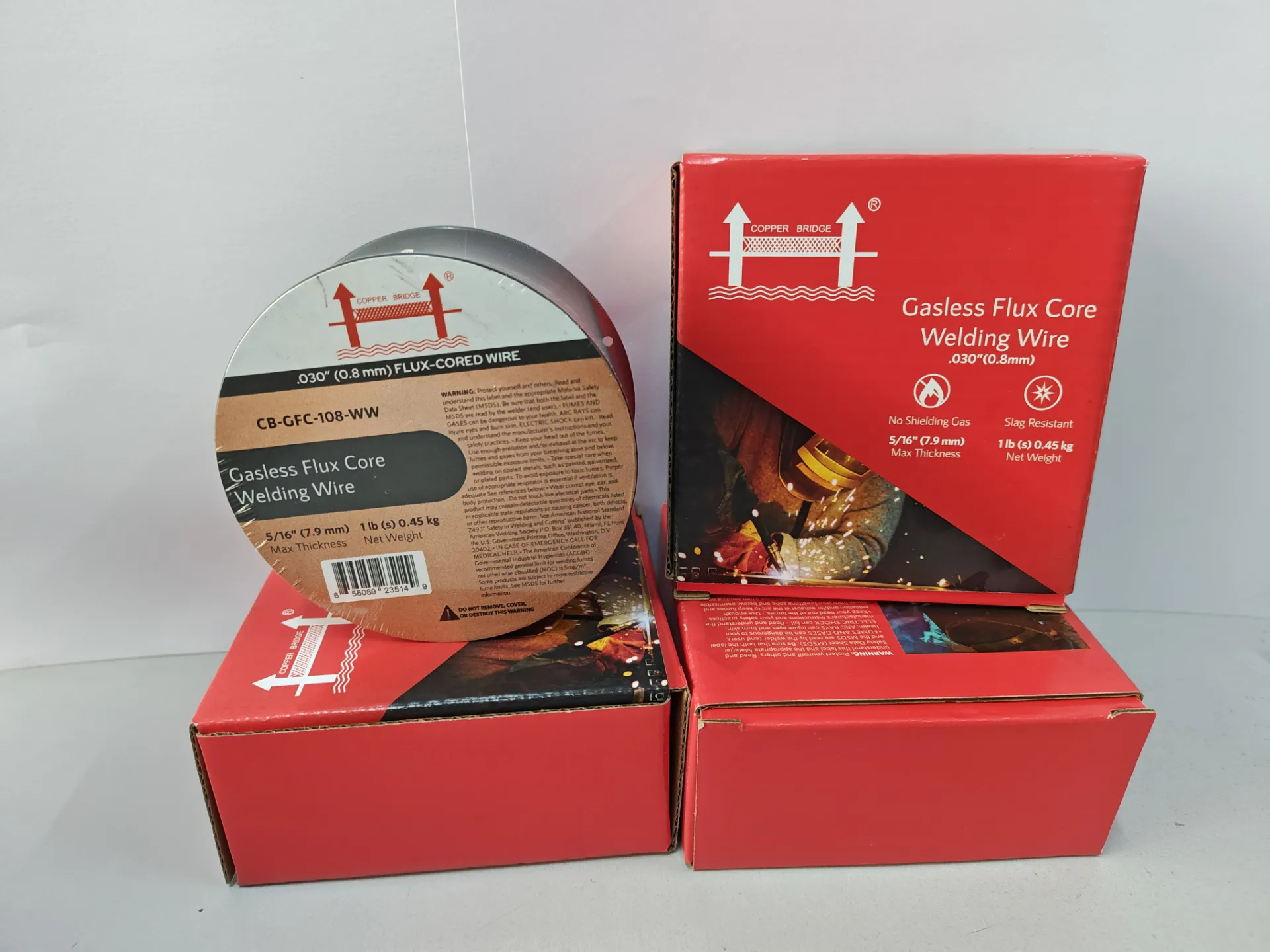
6010 welding rod amperage 3/32
Authoritativeness is underscored by the fact that the 6010 electrode is often recommended by industry leaders and welding certification entities for skill tests due to the precision and adaptability it demands from the welder. The electrode's deep penetration capability offers strong, secure welds, crucial in high-pressure conditions like pipeline construction. Welding instructors and professionals advocate for practice with the 6010 rod as it trains welders to control the puddle and adapt quickly to changing conditions, skills which are transferable to other welding scenarios and critical for certification purposes.
Trustworthiness is built through reliable information dissemination about welding techniques and rod specifications. The 6010 welding rod is a cellulose-coated electrode, particularly well-suited for dirty or oily metals due to its ability to penetrate through surface contaminants. Establishing trust involves not only sharing these properties but also reinforcing safe and effective use practices. Welders should be consistently reminded to wear appropriate personal protective equipment and ensure their work environment is conducive to safety and precision. The maintenance of equipment, especially ensuring a stable current flow from welding machines, is crucial for reliable performance with any electrode.
In conclusion, the 6010 welding rod at a 3/32-inch diameter is a versatile tool in the welder's arsenal when used with the appropriate amperage settings and technique. Through experience, expertise, and comprehensive understanding of this electrode's capabilities, welders can achieve high-quality results in various applications. The authoritative use of the 6010 rod exemplifies expert skill in managing complex welding projects, while trustworthiness is maintained by adhering to industry-standard practices that ensure both safety and performance excellence. Understanding these dynamics and applying them effectively is what transforms a good welder into an exceptional one.