Welding with a 55 nickel welding rod requires a harmonious blend of skill, knowledge, and precise technique. This alloy, primarily composed of nickel and iron, is renowned for its versatility and utility in various industries, especially in those demanding high thermal resistance and strength, like automotive and aerospace. Offering a unique combination of properties, these electrodes enable the welding of cast iron to itself and to other dissimilar metals, ensuring integrity and resilience in the finished product.
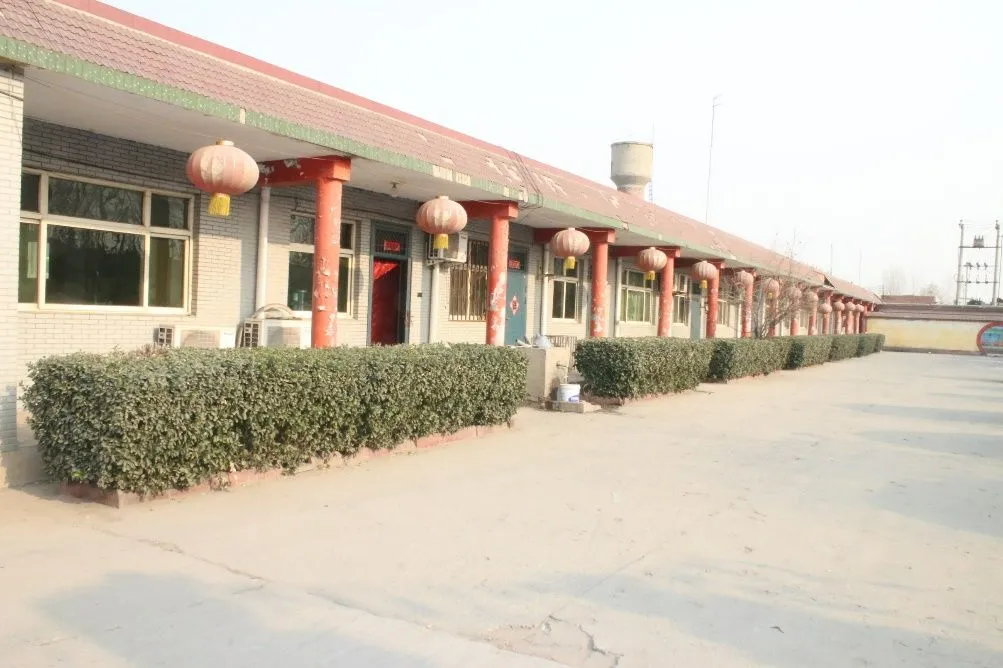
One of the critical aspects of using a 55 nickel welding rod is understanding its structural composition. The rods consist of about 55% nickel, which is ideal for welding components that are subject to constant thermal cycling, stress, or those that operate under extreme conditions. The added nickel content provides enhanced tensile strength and ductility, making the material less susceptible to cracking under stress compared to standard iron rods. This attribute is particularly critical when repairing or constructing high-value components such as heavy machinery gears and engine components.
Professional welders experienced with nickel alloy electrodes often emphasize the importance of pre-welding preparation. Cleaning the base metal thoroughly to remove all contaminants like oil, rust, or paint is crucial in achieving a sound weld. A wire brush or a chemical cleaner is frequently recommended to ensure that the surfaces are immaculate. An added layer of expertise involves pre-heating the workpiece, particularly for thick sections, to about 400°F. This practice helps in reducing thermal shock and the risk of cracking, which can be detrimental in high-stress applications.
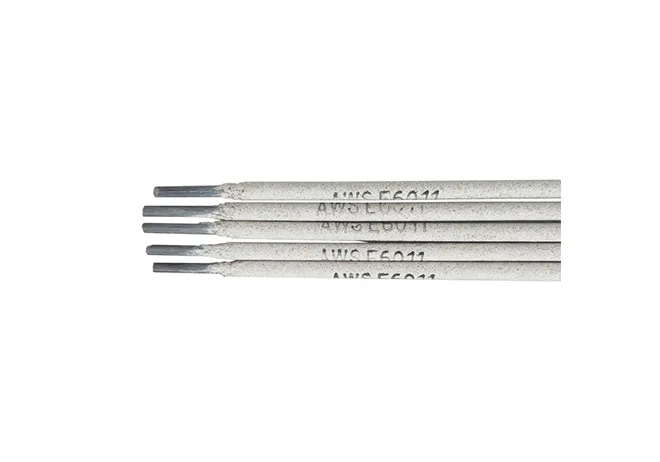
Another important consideration is the handling of the 55 nickel rods. Proper storage is vital to maintaining their pristine condition, avoiding exposure to moisture, which can lead to hydrogen embrittlement—a common cause of weld failure. Seasoned welders store these rods in a dry, temperature-controlled environment, preferring to use rod ovens or sealed containers to ensure they remain dry and free from atmospheric contaminants.
55 nickel welding rod
When it comes to technique, slow cooling is a paramount factor when welding with 55 nickel rods. Allowing the welded joint to cool naturally in air is a standard practice, which prevents the rapid cooling that can lead to brittleness and cracking. Some experts advocate for controlled cooling methods, such as covering the welded area with an insulating blanket, especially in colder environments to maintain an even temperature gradient.
Welding with nickel alloy rods may also necessitate specific welding machines that accommodate direct current electrode positive (DCEP) settings. Adjusting the machine settings to accommodate a lower amperage is usually advantageous as it provides better control over the weld puddle, ensuring penetration without excessive heat input that might lead to warping or structural weaknesses.
Trustworthiness is gained through testimonies from industry experts who have witnessed the enduring quality of welds executed with 55 nickel rods. Industries such as automotive restoration frequently share case studies where these rods have restored functionality to vintage engines, an endorsement of their reliability and engineering worthiness. Likewise, aerospace professionals praise these rods for their performance in maintaining the structural integrity of exhaust systems, where extreme temperature fluctuations are routine.
In conclusion, mastering the use of 55 nickel welding rods hinges on a comprehensive understanding of their properties, rigorous preparation, and precise application. They offer an unmatched fusion of strength and adaptability, critical for industries that cannot compromise on safety and performance. A deeper appreciation and adoption of these welding rods are likely to spur innovations in new sectors, providing further testament to their unmatched capabilities.