The welding industry is continually evolving, and staying informed about the nuances of different welding rods can make a significant difference in the quality and durability of your welds. One such essential welding rod that demands attention is the 6011 welding rod, especially when discussing the appropriate amperage settings for optimal performance. This article delves into the specifics of using 6011 rods and achieving that perfect weld.
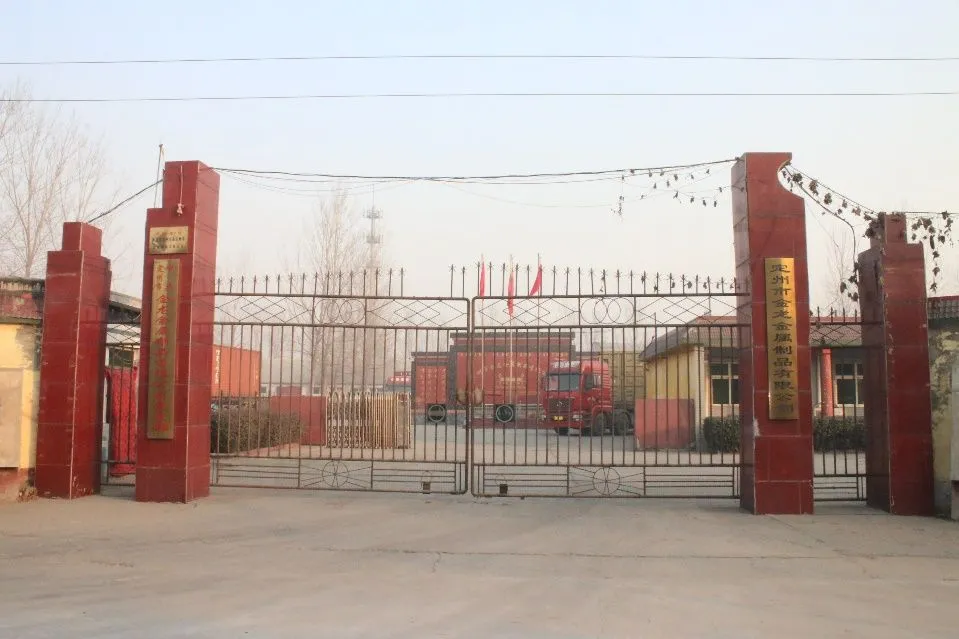
For starters, the 6011 welding rod is renowned for its versatility and ability to weld through rusty or dirty surfaces, making it a favorite among welders in various industries. This rod produces deep penetration, which is crucial for thick material and offers a high degree of reliability in adverse conditions.
When it comes to amperage, knowing the right settings is paramount to achieving a strong, aesthetically pleasing weld. The 6011 rods, commonly available in 1/8 inch diameter (equivalent to 3.2mm), typically run best within an amperage range of 75 to 125 amps on an AC welding machine, but the specific setting can vary based on factors such as the position of the weld and the thickness of the material you are working with.
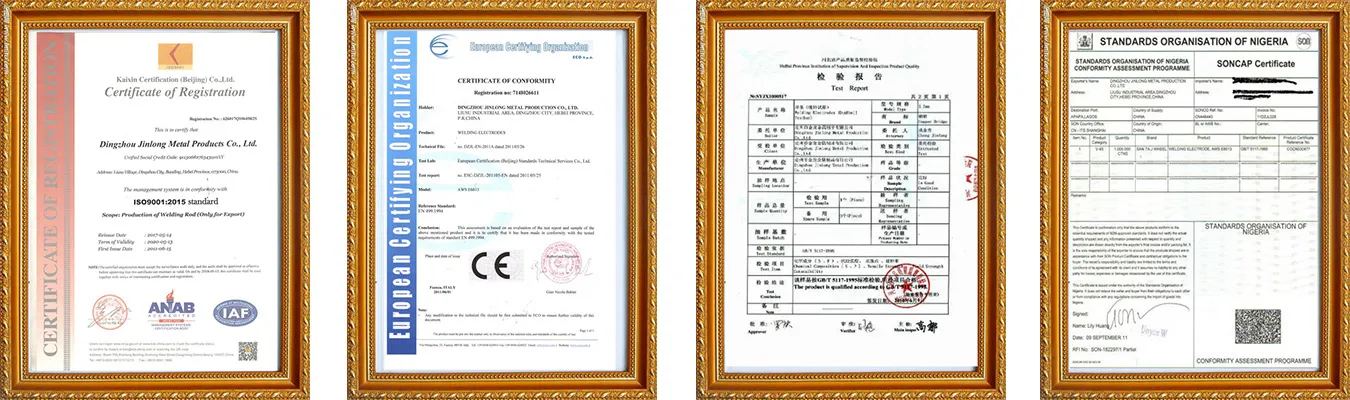
Experience dictates that for vertical or overhead welding positions, starting with a lower amperage can help manage the flow and puddle control, thereby reducing the likelihood of drips. On the other hand, when dealing with thicker materials or flat positions, a welder might need to push closer to the 125 amp range. This flexibility is one of the primary reasons why 6011 rods are favored in situations involving repair work, where the consistency of the surface might vary greatly.
Expert welders emphasize the importance of performing a test weld on scrap material before committing to critical work. By doing so, you can fine-tune the amperage settings to observe how the rod behaves under specific circumstances. This practice not only ensures the integrity of the weld but also bolsters the confidence of the welder, knowing that they have dialed in the optimal settings for the task at hand.
5 32 welding rod 6011 amperage
Another key aspect is the welding power source. The 6011 rods are compatible with both AC and DC welders, though they are traditionally more effective with an AC current. This compatibility provides welders the flexibility needed in the field or workshop and contributes to the rod’s popularity across different practice environments.
Authoritative voices in the welding community also point towards the importance of using reliable equipment. A high-quality welding machine can provide consistent and stable outputs, reducing the variance and improving the accuracy of your amperage settings. It's crucial to regularly maintain your welding machine to ensure it functions at its best, which in turn supports more precise control over your welds.
Trustworthiness extends beyond technical knowledge to include the safety precautions necessary when working with 6011 welding rods. Proper protective equipment (PPE), including gloves, helmets, and welding jackets, is non-negotiable. Additionally, ensuring that your workspace is well-ventilated will protect welders from harmful fumes and gases that arise during the welding process.
Finally, while the technicalities of the welding process are essential, creativity and feel are elements that cannot be overstated. Many experienced welders advise allowing the rod to ‘talk’ to you; observe the arc, listen to the sizzle, and feel the rod's feedback through your hand. This sensory input, combined with technical knowledge, ensures that each weld is precise and robust.
In conclusion, mastering the use of the 6011 welding rod involves understanding both the technical specifications and incorporating a personal touch that only experience can bring. By striking the right balance between science and art, welders can create superior welds that stand the test of time, irrespective of the challenges they face in the field.