In the niche world of welding, choosing the right tools and materials significantly impacts the quality of the work, safety, and efficiency of the operations.
One such crucial component of welding is the welding rod. When considering the specifications 347 16 welding rod, one delves into a category of consumables that enhances the welding process for specific types of stainless steels. Here’s an exploration of the intricacies of using a 347 16 welding rod, ensuring a deep understanding for both professionals and hobbyists in the field.
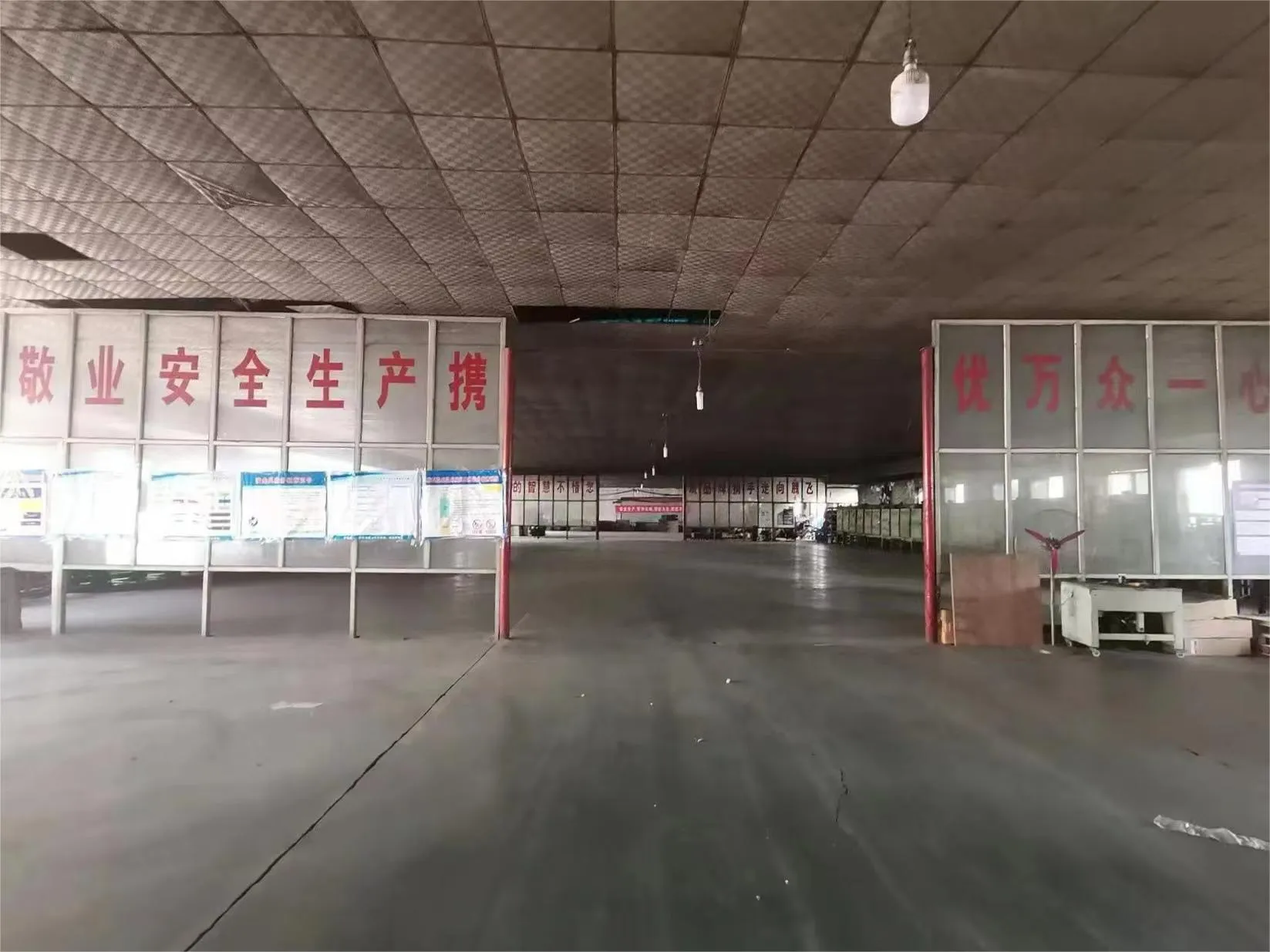
To comprehend the benefits and applications of a 347 16 welding rod, it is essential to understand what the numbers signify. The 347 designation refers to a type of stabilized stainless steel, especially designed to withstand intergranular corrosion. This is achieved by adding niobium which acts as a stabilizer, effectively allowing the rod to manage the high temperatures encountered during welding processes without precipitating carbides at the grain boundaries. On the other hand, 16 represents the rod’s coating type and compatibility with various welding currents, indicating it's chiefly used with alternating current (AC) and direct current electrode positive (DCEP).
Experts in welding consistently emphasize the importance of matching welding rods with the base metal being welded to ensure the best possible bond and structural integrity. The 347 16 rod is particularly adept at welding types 321 and 347 stainless steels, offering capabilities that make it suitable for high-temperature applications such as chemical processing equipment, heat exchanger tubes, and steam pipes. This makes it a versatile choice for industries where both longevity under stress and resistance to corrosion are paramount.
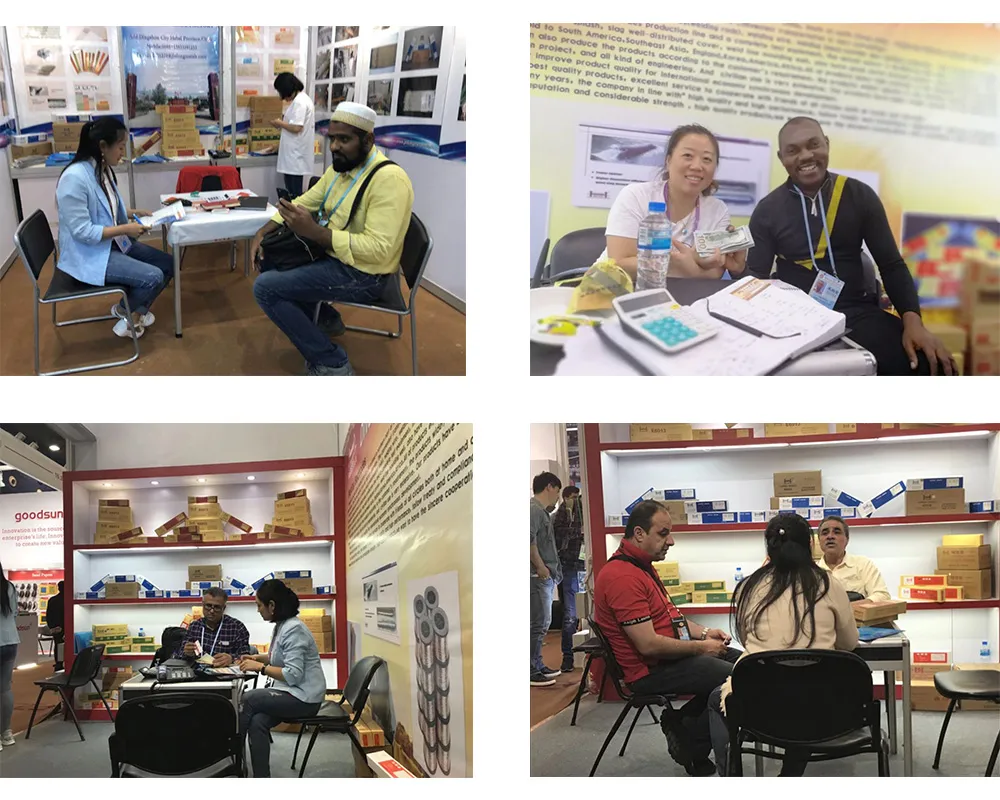
A unique characteristic of the 347 16 welding rod is its resistance to intergranular attack, a common issue that can compromise welds exposed to high temperatures. Experience from industry professionals showcases that when welding with 347 16 rods, the finished welds are more robust against the detrimental chromium carbide precipitation. This reduction in susceptibility means longer-lasting welds, decreasing the need for frequent maintenance and replacements.
From an expert standpoint, using 347 16 welding rods requires an understanding of specific welding parameters to maximize the benefits. Optimal results involve maintaining proper heat inputs and ensuring a controlled cooling rate. Excessive heat can reduce the rod’s stabilizing effects and potentially increase the risk of carbide precipitation. Trustworthy techniques from seasoned welders also include pre-welding preparations such as cleaning the base metal, which ensures impurities do not hinder the welding process.
347 16 welding rod
Moreover, authoritative sources in welding standards offer guidelines for proper rod storage to avoid contamination. 347 16 rods should be kept in a controlled environment to maintain their integrity. Moisture is a notorious enemy to welding rods, as it can lead to hydrogen inclusion in the welds, diminishing their quality. Professional guidelines suggest storing these rods in a dry area and using a rod oven if necessary to preserve their usability.
Anecdotally, those with years of welding experience often speak to the adaptability of the 347 16 rod in various environments and temperatures. For instance, in shipbuilding and repair, where high durability and corrosion resistance are required, this rod proves indispensable. Similarly, experts recommend the 347 16 rod for welding components in power generation plants where high thermal resistance is a critical factor.
Nevertheless, mastery over welding also involves understanding potential challenges. Some welders report that handling specific angles or working with confined spaces can present challenges unique to 347 16 rods’ thicker coatings. Experience highlights the need for deliberate practice in different scenarios to overcome these hurdles.
In summary, the 347 16 welding rod stands out in the welding industry not merely due to its physical properties but because of the expertise it allows professionals to display in high-stakes environments. For those vested in achieving optimal results in their work, incorporating this rod means embracing both the science and art of welding, ensuring not only efficient and quality welds but also reinforcing trust in every joint made.