3/32 stick welding rods are an integral component of any welder’s toolkit, particularly when dealing with specific jobs that require precision and reliability. As welders search for methods that optimize their craft, understanding how to effectively use 3/32 welding rods enhances both skill and output quality, cementing a welder’s professional reputation.
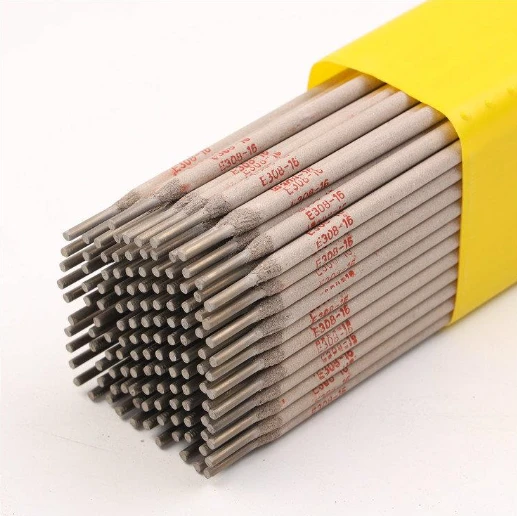
Experienced welders often prefer 3/32 stick welding rods due to their balance of size and heat production capability. The specific diameter allows for high precision in welding processes, especially useful for thinner material applications where larger rods may yield inconsistent welds. Mastery of these rods requires not only technical know-how but also a set of refined skills that develop over time with practice and exposure to varied welding scenarios.
Expertise in welding with 3/32 rods involves noticing the nuances of different metals and their reactions to heat and filler materials. Welders with a professional demeanor understand that each electrode, or rod, is designed for certain specifications. The intricacies of these rods are known to those with specialized training, as they are crafted to work optimally within specified amperage ranges—typically between 40 and 90 amps for 3/32 rods. This range is crucial for maintaining bead control and penetration consistency, especially in vertical and overhead positions where welding precision is paramount.
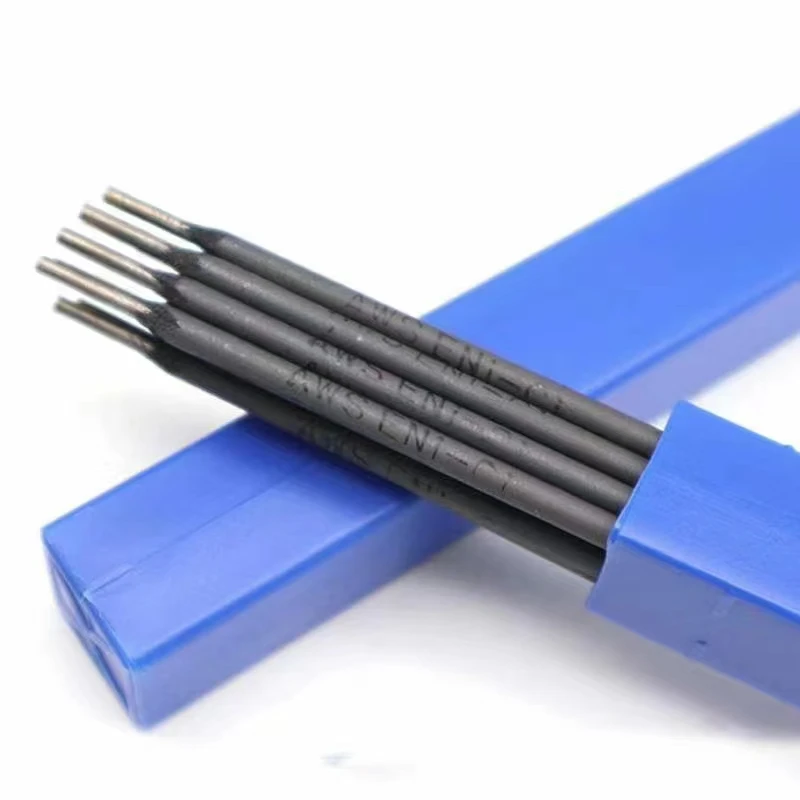
For those with an authoritative voice in the welding community, advocating for 3/32 sticks becomes a natural extension of promoting optimal welding technique. These experts underline the importance of proper storage and handling to maintain the integrity of the welding rod coating, which affects everything from arc stability to the aesthetic quality of the weld. Moisture, a formidable enemy of coated electrodes, can compromise flux effectiveness. Therefore, these rods are best kept in environments with controlled humidity and temperature, further illustrating the importance of protective measures informed by authority-driven insights.
3/32 stick welding rods
Trustworthiness in using 3/32 welding rods can be primarily established by adhering to safety standards and best practices. Responsible welders prioritize safety by wearing appropriate protective gear such as gloves, helmets, and flame-resistant clothing. The reliability of these rods pairs with the welder’s responsibility to adhere to safety guidelines, ensuring both personal safety and the structural integrity of the welds produced. Moreover, utilizing reputable brands and supplier sources for acquiring 3/32 rods guarantees consistent quality and adherence to industry standards, which is vital for maintaining trust in one’s welding operations.
Understanding the compatibility of 3/32 welding rods with specific materials is another cornerstone of using these rods effectively. They perform exceptionally well with mild steel but are also adept at adhering to specific types of stainless steel and cast iron given the correct conditions and rod compositions. To fully leverage the potential of 3/32 rods, welders must assess the base material with a critical eye, recognizing the nuances of metallurgical properties and adjusting their technique accordingly.
The practice of welding with these particular rods also involves strategic decisions around positioning and motion.
Achieving an optimal weld profile with 3/32 rods often requires a balance between travel speed and rod angle. A common tactic among seasoned professionals is the use of a slight whip and pause motion that promotes consistent heat distribution and optimal bead formation. This refined approach contributes to better mechanical properties of the completed joint, demonstrating the technical acumen that separates proficient welders from novices.
Overall, 3/32 stick welding rods represent an intersection of technical prowess and practical application within welding. Engaging with these tools requires a mix of experience-driven insights, precise technical execution, authoritative guidance on application techniques, and a strong commitment to safety and quality standards. Through continued education and practice, welders can cultivate expertise in utilizing 3/32 rods, reinforcing their professional stature and contributing to advancements in the field.