The 3/32 nickel welding rod stands as a pillar of reliability and efficiency within the world of welding. This staple product is often the unsung hero of robust metalwork projects, providing both strength and flexibility. Whether you are a seasoned welder or a newcomer eager to hone your craft, understanding the merits and proper usage of the 3/32 nickel welding rod can elevate your work to new heights.
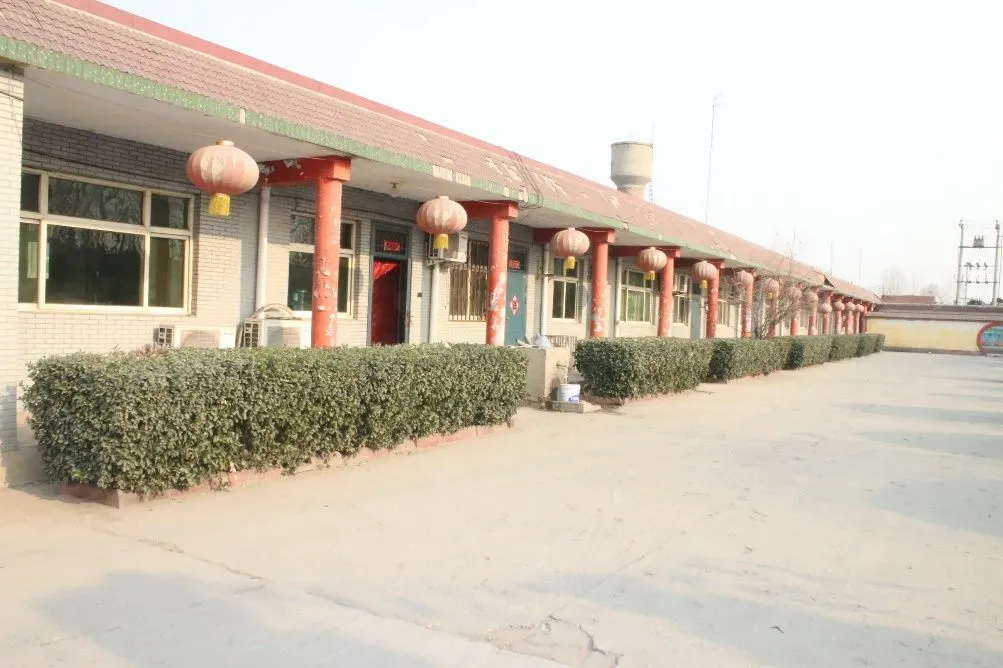
Nickel welding rods, by their very nature, are versatile and suitable for a myriad of metal joining scenarios.
What makes the 3/32 variant particularly special is its balance. This specific size is incredibly handy for precise applications, making it a go-to for many tasks where other rods might falter. Its slim profile allows for fine work in confined spaces and intricate projects without compromising the overall strength of the weld.
Experience from seasoned welders emphasizes the importance of rod selection according to the project needs. The 3/32 nickel rod excels in joining nickel alloys and steels due to its superior corrosion resistance and mechanical properties. These attributes make it indispensable in industries such as aerospace, marine, and chemical processing where durability and environmental resistance are critical.
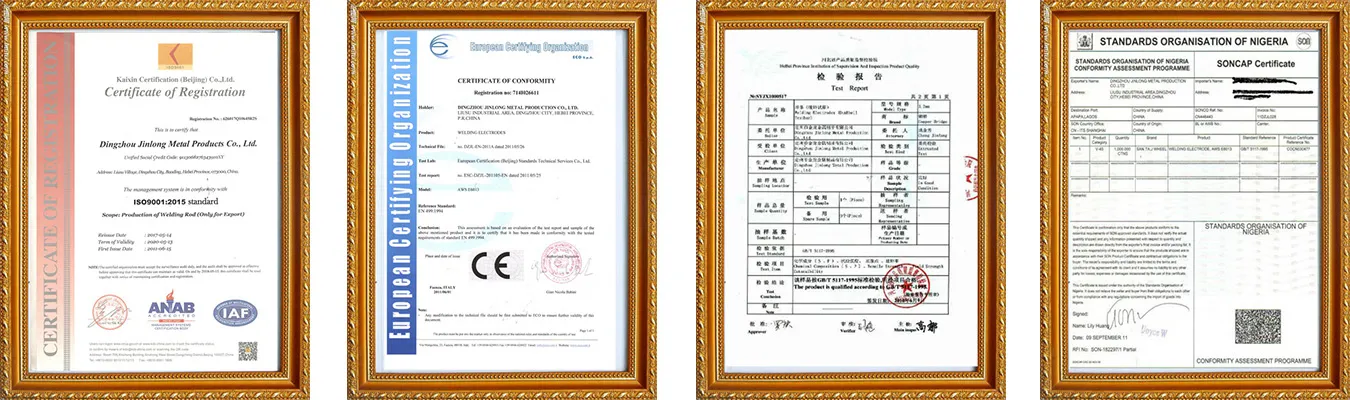
The expertise of professionals in the field indicates that preparation before welding plays a crucial role. Cleaning the metals to remove any oil, grease, or rust ensures the integrity of the weld. Experienced welders often employ a slight weave technique when working with 3/32 nickel rods, allowing for a flat and visually appealing weld bead. Mastering the correct heat and speed settings is also vital, as nickel conducts electricity differently compared to other metals.
From a technical standpoint, the 3/32 nickel welding rod operates optimally with DC positive polarity. The arc stability and ease of striking with these rods make them a favorite among welders looking to achieve smooth and consistent results. With proper technique, the welds produced are not only robust but also aesthetically pleasing, an essential trait for any project where visual presentation is just as important as durability.
3/32 nickel welding rod
Manufacturers and industry experts frequently highlight the importance of maintaining welding equipment and adapting settings to suit the specific task when using these rods. Ensuring the welding machine is correctly calibrated can prevent common issues like cracking or porosity that might compromise the weld's strength.
The authoritativeness of the 3/32 nickel welding rod is reinforced through its widespread adoption in demanding environments. Welding instructors and industry veterans advocate for its use as a teaching tool, serving as an excellent foundation for learners due to its forgiving nature and adaptability in diverse situations.
Trustworthiness in weld quality is paramount, and with the 3/32 nickel welding rod, confidence in the final product is virtually guaranteed. This type of welding rod is often certified to meet rigorous industry standards, ensuring that professionals can rely on its consistency and reliability from batch to batch. This assurance is critical for projects where safety and performance are of utmost importance.
Overall, the 3/32 nickel welding rod represents the confluence of precision, strength, and reliability. Its unique attributes cater to both the novice welder who seeks to learn and the seasoned professional who requires impeccable results. Its rightful place in the toolkit of any welder is undisputed, bringing together years of welding expertise and technological advancement. By understanding and respecting the nuances of this product, welders can achieve superior outcomes that stand the test of time.