The use of 3/32 aluminum welding rods can transform amateur projects into professional-grade achievements, provided that the right techniques and expertise are applied. As welding aluminum is notoriously difficult, it demands a profound understanding of both the materials and the tools involved.
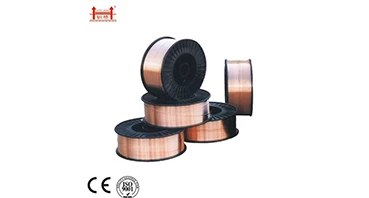
Aluminum, unlike steel, requires precise handling due to its lower melting point and the potential for oxide formation, which hinders the welding process. The 3/32-inch welding rod is particularly suited for this task, offering a perfect balance in thickness for various aluminum welding applications, from marine projects to automotive engine parts.
An experienced welder knows that the initial step involves thorough cleaning of the aluminum surface. Oxidized layers form swiftly on aluminum when exposed to air, thereby necessitating the use of a stainless steel wire brush or dedicated aluminum cleaner right before welding.
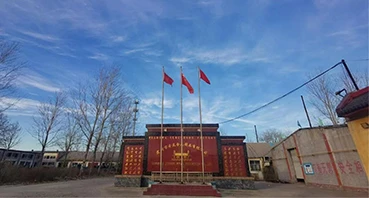
Positioning and settings are the next critical components. Utilizing a TIG (Tungsten Inert Gas) welding process ensures better control over the weld than the alternatives like MIG (Metal Inert Gas). When using a 3/32 aluminum rod, it’s advisable to set the welding machine appropriately—often a frequency of around 120 Hz offers increased penetration and a smoother arc. The machine should be set to AC mode because aluminum requires higher heat than DC setups provide.
Equipped with a suitable TIG welding torch, ideally with a 3/32 tungsten electrode to complement the rod size, one can achieve cleaner welds with minimal spatter. The user must ensure that the torch angle is maintained correctly, at approximately 15 to 20 degrees from vertical, allowing for optimal gas coverage without turbulent airflow that might contaminate the weld pool with oxides or impurities.
3 32 aluminum welding rod
Real-life experience reiterates the importance of selecting the proper filler metal, which cannot be overstressed. Pure aluminum (1100 series) is softer and more forms a ductile weld, beneficial for applications that require rust resistance rather than strength. On the contrary, 4043 rods are a go-to for crafting stronger joints that can withstand significant stress despite the different thermal expansion rates of aluminum alloys.
Safety is a paramount concern when working with aluminum welding. The increased brightness of the aluminum arc requires that the welder wear protective gear that goes beyond the basic welding helmet. Special UV protective clothing may be necessary to prevent burns from arc exposure.
Building trust with audiences interested in aluminum welding comes from transparent communication. Sharing personal stories of welding success enhances credibility. Whether it’s refurbishing an old aluminum boat or assembling custom aluminum bicycle frames, each project demonstrates the versatility and necessity of the 3/32 welding rod in achieving professional results without compromising the integrity of the aluminum material.
Knowledge-sharing through tutorials and workshops further solidifies authority status in the field. Proactive engagement with the community—perhaps through online forums, social media channels, or even local hardware store clinics—expands the reach and influence of any welding expert or business. Posting detailed guides and how-to videos also ensures visibility for those searching for specific aluminum welding solutions.
In summary, mastering aluminum welding with 3/32 rods demands not just the right tools but a bank of knowledge accumulated through both study and practical application. It’s in the attention to detail – from selecting the correct filler rod to maintaining the ideal settings on a TIG machine, and embracing safety protocols – that both quality and efficiency are realized. An authoritative, credible, and trust-building approach will invariably lead to enhanced recognition and respect within the welding community, setting the standard for others to follow.