The 330 stainless steel welding rod offers a remarkable choice for specialized welding applications, especially in environments that demand superior resistance to high temperatures and corrosive materials. This blog dives into the unique attributes, applications, and expert handling tips of the 330 stainless steel welding rod, ensuring an authoritative guide for those seeking to master its use.
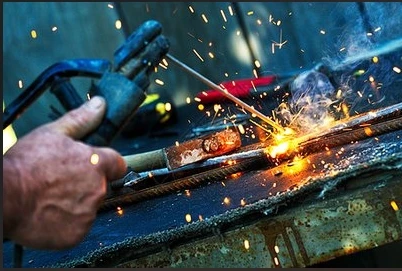
330 stainless steel is distinguished by its high chromium and nickel content, which confers outstanding resistance to oxidation and carburization at elevated temperatures. The welding rod made from this alloy is not just ideal for joining 330 stainless steel surfaces but also for welding dissimilar steels with comparable thermal expansion properties. This versatility makes it indispensable in industries that operate under extreme conditions, such as petrochemical manufacturing, thermal processing, and high-temperature furnace construction.
When welding with 330 stainless steel rods, understanding the material’s thermal behavior is crucial. The high nickel content reduces thermal expansion, while the chromium component ensures oxidation resistance. Such properties require precise control over welding parameters to prevent warping or distortion, ensuring seam integrity and longevity.
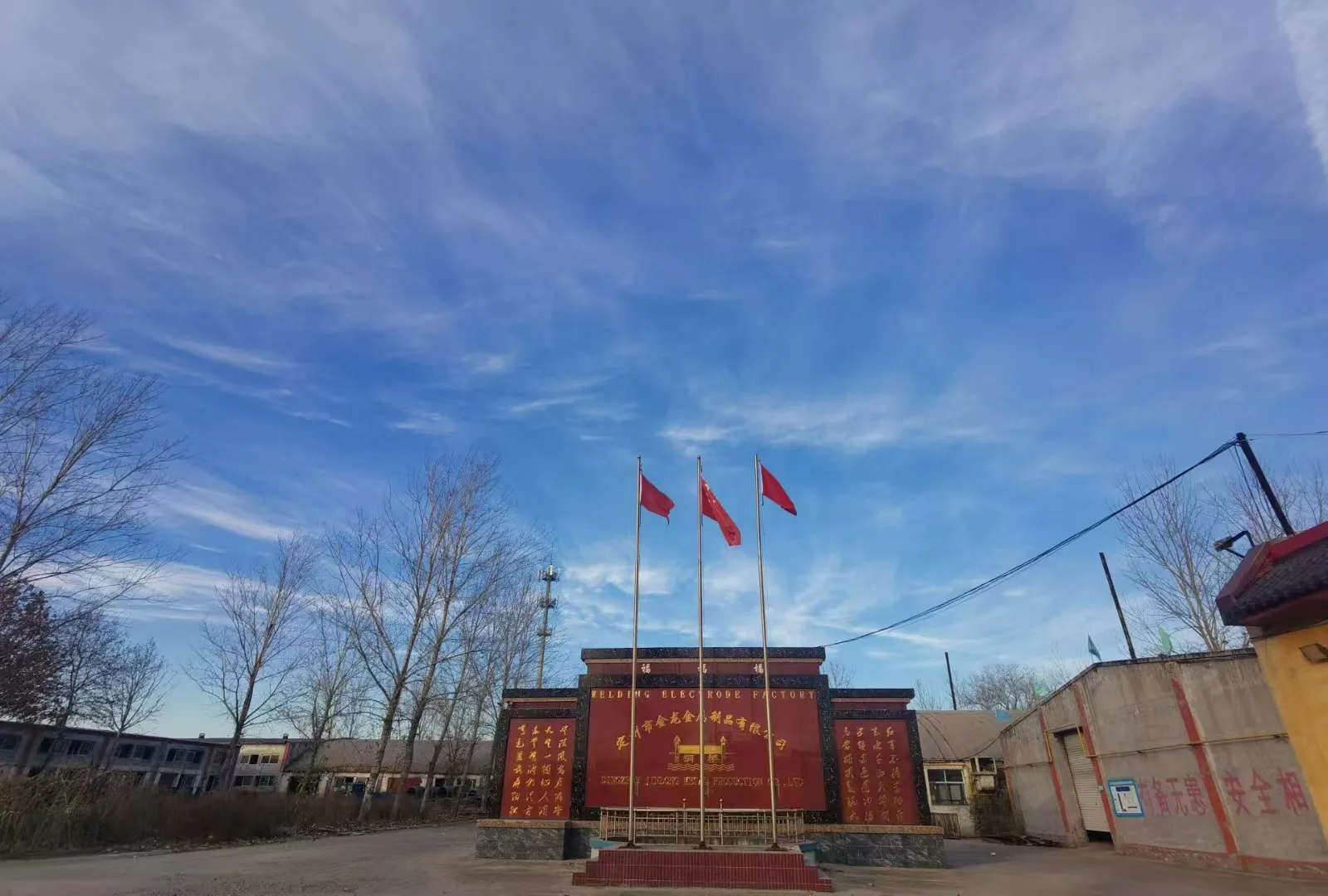
For those new to welding with 330 stainless steel, beginning with smaller, well-contoured weld beads minimizes the heat input, effectively reducing thermal stress and deformation. Employ a low-amperage setting initially to avoid excessive heat build-up, which could compromise the structural properties of the material. Furthermore, maintaining an appropriate travel speed is essential; too slow a speed might overheat the material, whereas too fast could lead to inadequate fusion.
Expertise in pre-weld and post-weld treatments is vital. Pre-weld joint preparation is foundational in achieving optimal results. Ensure the surfaces are meticulously cleaned of contaminants such as oil, grease, and dust. Preheating, though often unnecessary due to the alloy’s forgiving nature, can be advantageous in thick sections or highly restrained joints to prevent cracking.
330 stainless steel welding rod
Post-weld heat treatment generally involves annealing to stress relieve the weld areas, enhancing toughness and reducing brittleness. This is particularly relevant in sections that experience dynamic loading or rigorous thermal cycling.
The application environment heavily influences the choice of welding rod, and the 330 variant is no exception. Engineers and metallurgists will frequently turn to this alloy when designing components for applications facing constants near 2000°F (1093°C). This makes it ideal for furnace components, muffles, and retorts in heat-treating industries. Its ability to withstand sulfur-bearing gases without compromising structural integrity further extends its use in chemical processing equipment.
Ensuring the trustworthiness of any welding process involves thorough documentation and adherence to industry standards such as those set by the American Welding Society (AWS). Using certified rods from reputable manufacturers ensures the material consistency and quality necessary for critical applications. Additionally, routine inspections and quality assessments of the welds are essential for maintaining ongoing reliability and understanding material behaviors under operational stresses.
Employing 330 stainless steel welding rods can significantly enhance the performance and service life of high-temperature assemblies. Their remarkable properties require an expert’s touch to unlock their full potential, from the thoughtful selection of welding parameters to rigorous post-weld inspections. For industries that operate under high-stakes conditions, the judicious use of such specialized welding materials supports not just productivity but also safety and longevity, ensuring that structural failures are averted and operational excellence is achieved.