Elevating Welding Projects with the 312 SMAW Electrode
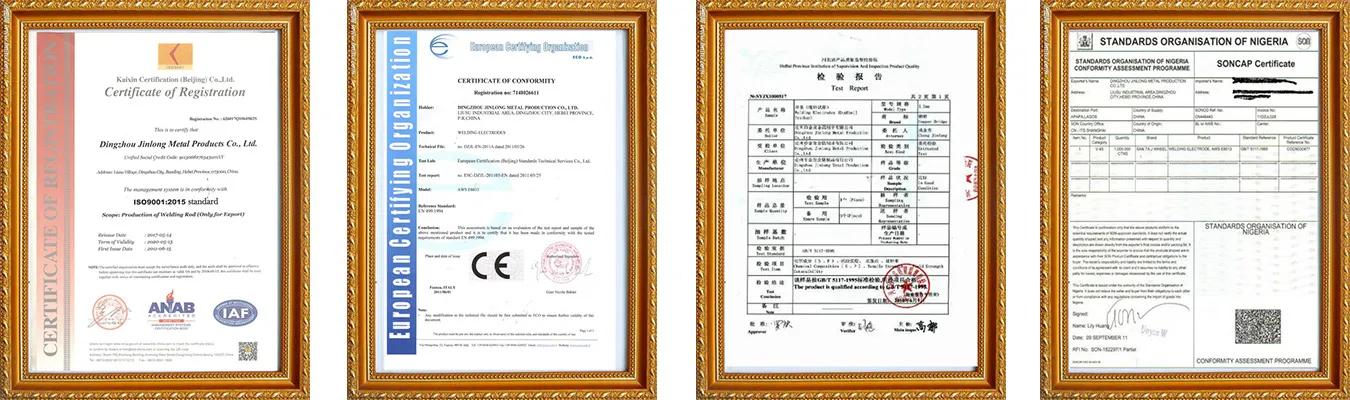
The 312 SMAW (Shielded Metal Arc Welding) electrode is an indispensable tool for welders who demand precision, durability, and reliability. Recognized for its robust capabilities, this electrode is often preferred for complex welding tasks requiring superior join strength and resistance to thermal cycling. The knowledge and expertise surrounding the optimal use of the 312 SMAW electrode can significantly enhance both the quality of the welds and the efficiency of the welding process.
Renowned for its high nickel content, the 312 SMAW electrode exhibits exceptional resistance to cracking and corrosion. This attribute is particularly valuable when dealing with dissimilar metals, where standard electrodes might fail to maintain integrity under stress. The alloy’s versatility extends to a variety of metal combinations, including joining stainless steel to carbon steel, making it a superior choice for welders dealing with diverse material requirements.
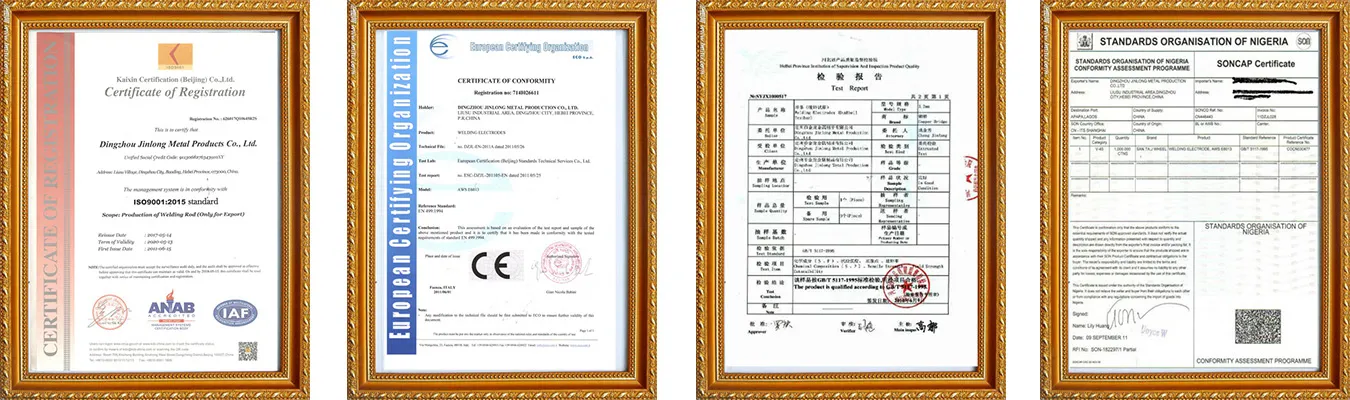
Professional welders appreciate the 312 SMAW for more than just its physical properties. The electrode's performance in adverse conditions sets it apart. Its ability to create stable arcs and deliver easy slag removal streamlines the welding process, saving both time and effort. This is particularly critical in industrial applications where time constraints and specific quality standards must be met.
Experts in the field highlight the electrode's application in high-temperature environments, such as those encountered in the petrochemical and power generation industries. Its resistance to scaling ensures welds maintain their integrity even under continual thermal stress. This makes the 312 SMAW a preferred choice for constructing and repairing high-pressure vessels and pipelines, where safety is paramount.
312 smaw electrode
In terms of usability,
the 312 SMAW electrode offers considerable flexibility. Its compatibility with both AC and DC currents gives welders the freedom to optimize their machinery setup based on the specific demands of a project. This versatility allows for greater adaptability across different welding scenarios, enhancing the welders' ability to deliver high-quality results consistently.
The electrode's ease of use is also complemented by its chemical stability, which ensures consistent performance across varying environments. This stability reduces the likelihood of post-weld defects such as spatter and porosity, which can compromise the final product's structural integrity. For projects requiring a polished finish, the 312 SMAW's smooth bead appearance reduces the need for extensive post-weld processing, ultimately saving time and costs.
However, to fully leverage the benefits of the 312 SMAW electrode, welders must possess a thorough understanding of its handling characteristics and best practices. Expertise in pre-heating and cooling techniques, alongside knowledge of optimal storage conditions, can prevent moisture absorption which could adversely affect performance. A skilled hand coupled with detailed procedural knowledge ensures the electrode's full potential is realized.
Training programs and certifications focusing on the 312 SMAW electrode underscore the importance of safety and precision. These programs nurture a deeper understanding of metallurgical principles, equipping welders with the insights needed for complex projects. Certified professionals are better equipped to deliver work that meets stringent industry standards, enhancing trust and credibility with clients.
Ultimately, the 312 SMAW electrode is not just a tool, but a cornerstone in the repertoire of professional welders. Its proven track record and advanced capabilities make it indispensable in today’s industrial landscape. By understanding its properties and applications, welders can unlock new possibilities in metal fabrication, ensuring superior performance and long-lasting results. Embracing the 312 SMAW is an investment in quality, precision, and craftsmanship — an unwavering testament to expertise in the art of welding.