When delving into the world of welding, selecting the right materials is pivotal for achieving durable and high-quality results. The 310 16 welding rod has emerged as a prominent choice among professionals, acclaimed for its exceptional properties. Unlike several other rods, the 310 16 is specifically crafted to offer superior resistance to oxidation and corrosion, making it an expert tool in demanding environments. With its unique composition, this welding rod proves indispensable in both professional workshops and industrial applications.

The advanced engineering of the 310 16 welding rod sets it apart as a robust solution for welding stainless steels, particularly those rich in chromium and nickel. Its credentials are backed by a series of well-documented performance tests in high-temperature settings. Whether building components for power plants or repairing industrial furnaces, this rod ensures that the welds maintain integrity even when subjected to severe conditions. One real-world application saw a manufacturing unit using the 310 16 rod to join stainless steel parts of an exhaust system, achieving results that exceeded industry standards in thermal cycling resistance.
An informed decision in welding doesn't stop with choosing a premium product like the 310 16 welding rod; it demands understanding its specific utility. Experts confirm that this rod is ideal when the project involves extensive exposure to intense heat or corrosive elements. The rod's chemical formulation, with its high chromium content, directly contributes to its ability to prevent scaling, ensuring that the structural and aesthetic qualities of the weld remain intact over time. This makes it particularly advantageous in construction projects involving architectural steelwork, where both strength and appearance matter.
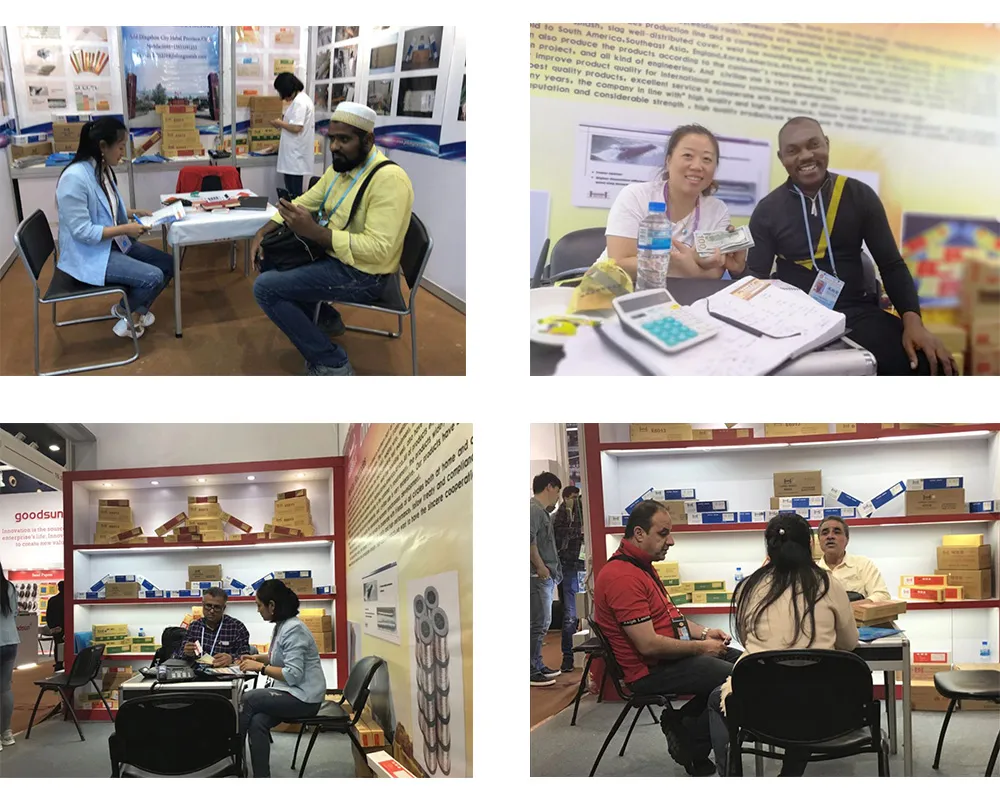
Professionals consistently emphasize that while the rod’s performance is commendable, its correct usage is equally crucial.
Proper technique and welder experience significantly affect the outcome. Welding experts recommend maintaining a stable arc and controlling the deposition rate to optimize the rod's effectiveness. When adhered to meticulously, these practices ensure the weld is not just functionally reliable, but also aligns with stringent industry safety standards. Such authoritative guidance assures clientele that partnering with experienced welders will secure both desired results and safety compliance.
310 16 welding rod
Trust in the 310 16 welding rod is reinforced by its widespread endorsement across industries. Structural engineers and fabricators prefer this rod due to its proven track record in projects requiring high structural integrity. Its compatibility with various welding machines also broadens its scope of application, making it a versatile asset for any welding professional looking to elevate their service offerings.
Building on the characteristic strengths of the 310 16 rod, feedback from seasoned users highlights its economic advantage. While its initial cost might be higher than some alternatives, its longevity, minimal maintenance demands, and the reduced need for repair rework offset the expense. This cost-efficiency narrative resonates with businesses striving for sustainable operations without compromising on quality or performance.
In summary, the 310 16 welding rod stands as a testimony to advances in welding technology, providing a combination of strength, resistance, and reliability. Its meticulous engineering offers unparalleled performance, especially in high-stakes projects requiring robust and durable welds. Recognizing its merits, leveraging professional expertise for its application, and ensuring an adherence to industry best practices collectively affirm its place as a trusted choice for welding excellence. For those committed to delivering enduring quality and reliability in their welding projects, the 310 16 welding rod is an investment in expertise and trustworthiness.