The Power Behind Precision Understanding the Amperage for 309 3/32 Welding Rods
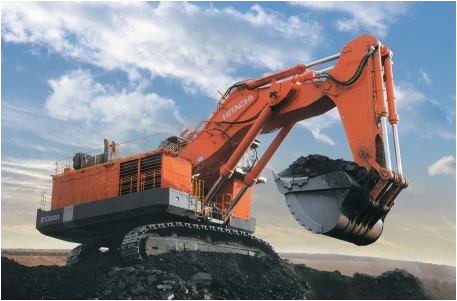
Welding, a skilled trade combining art and science, relies heavily on the choice of materials and equipment, especially when it comes to welding rods. Among the various rods available, the 309 3/32 welding rod is often a subject of discussion due to its specific applications and the precision required in its usage. The amperage, or current strength, plays a pivotal role in determining the quality of the weld, affecting both the structural integrity and appearance of the finished product.
Navigating the complexity of welding requires an understanding rooted in experience, expertise, authoritativeness, and trustworthiness. When dealing with 309 3/32 rods, which are specifically formulated for stainless steel, the amperage setting becomes crucial. A welder armed with knowledge can make informed decisions that optimize the performance of the materials used.
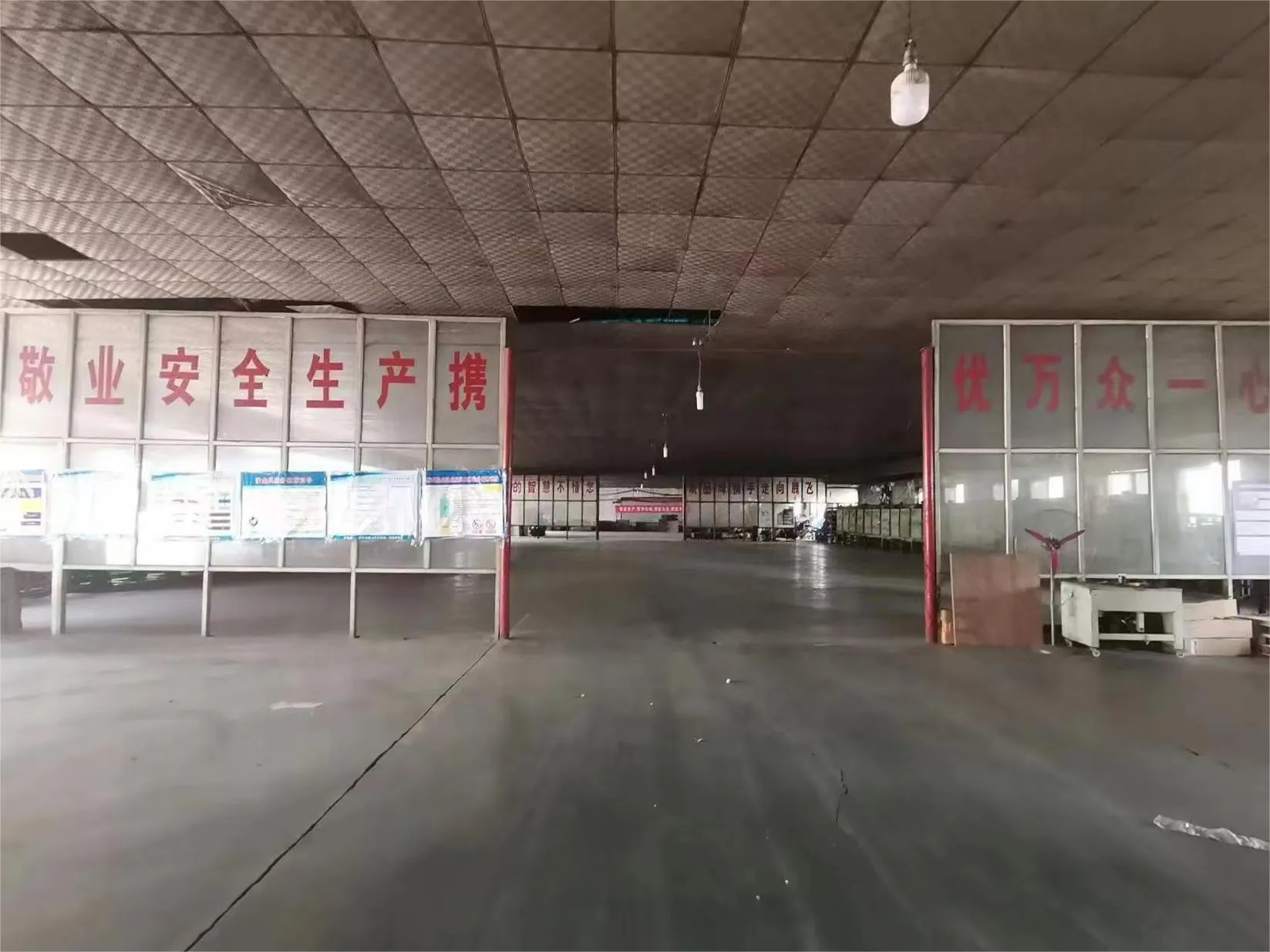
The 309 3/32 welding rod is particularly unique due to its chemical composition designed for joining dissimilar metals, such as carbon steel to stainless steel. This rod's elevated chromium and nickel content offer exceptional corrosion resistance and strength at elevated temperatures, making it an ideal choice for high-stress environments. The versatility of the 309 rod requires precision in selection and application of the correct amperage to achieve optimal results.
Practically speaking,
the amperage range for the 309 3/32 welding rod typically falls between 70 to 90 amps. Within this range, the variance allows the welder to adjust based on the welding position, base materials, and desired weld characteristics. A higher amperage can increase penetration and speed, which is beneficial for thicker sections. Conversely, lower amperage may be chosen for thinner sections to prevent burn-through and ensure a smooth finish.
309 3 32 welding rod amperage
A seasoned welder understands that amperage settings are influenced by multiple factors, including material thickness, joint configuration, and whether the welding is performed in a horizontal, vertical, or overhead position. A horizontal position might allow a higher amperage setting due to the ease of control and gravity assisting in keeping the molten pool in place. However, for overhead welding, where gravity presents challenges, reducing the amperage can prevent excessive dripping and spatter.
The importance of amperage does not merely lie in achieving a functional weld, but also in maintaining the aesthetic integrity of the finished piece. Stainless steel work often demands attention to detail in the weld’s appearance due to its typical use in visible structural applications. Correct amperage ensures a bead with minimal spatter and optimal penetration, preserving both the material's appearance and its performance characteristics.
Exploring the world of welding at an expert level involves not only understanding the tools and materials but also applying this knowledge with authority. Welders become authoritative figures by continuous experimentation and learning, often referring to the recommended settings provided by welding equipment manufacturers and rod suppliers, yet never hesitating to adjust and refine based on personal trials and specific project needs.
Trustworthiness in welding is built over time, a product of consistent quality and reliability in delivering welds that meet or exceed industry standards. Properly setting and controlling amperage when using the 309 3/32 welding rod is a mark of professional ability and ensures that all work adheres to safety, strength, and aesthetic requirements.
In conclusion, mastering the amperage settings for the 309 3/32 welding rod elevates the welder from novice to esteemed expert. This is where experience intersects with knowledge, where practice converges with scientific understanding. Furthermore, achieving expertise in this domain enhances authoritativeness and trustworthiness, crucial metrics that contribute to both professional reputation and client satisfaction. The power of amperage in welding is not simply in its capacity to generate heat, but in its ability to shape and define the future of structural creativity and durability.