Navigating the realm of welding requires understanding the complexities of different tools and materials, one of which is the 309 3/32 welding rod. Known for its unique properties, this welding rod holds specific requirements, particularly when considering the amperage settings necessary for optimal performance. Drawing from deep expertise in welding, it's paramount to explore the nuances of this rod's functionalities to achieve peak outcomes while maintaining safety and material integrity.
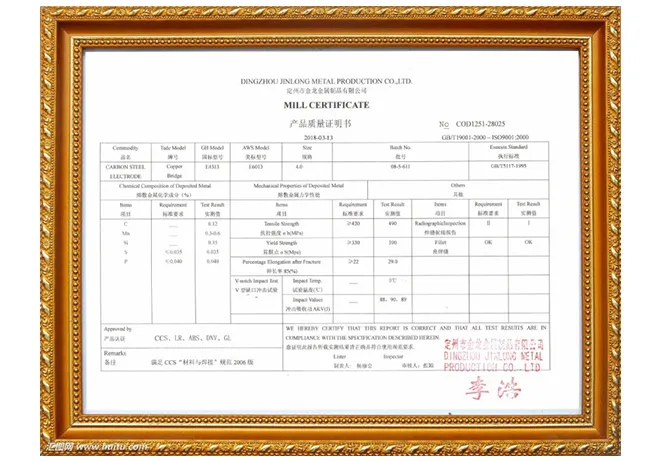
The 309 3/32 welding rod stands out for its superior versatility, especially suited for joining dissimilar metals, frequently deploying in welding stainless steel to carbon steel. Its composition of 23-25% chromium and 12-14% nickel lends it the robustness to handle the thermal stresses involved in such processes. When discussing amperage settings, expert welders emphasize the importance of precision. The rod typically requires an amperage range between 75 to 110 amps, depending on the thickness and type of the metals being welded. For those new to the craft, standing within the mid to upper range is beneficial as it provides a stable arc without compromising penetration or bead quality.
Trustworthiness in handling this rod comes from acknowledging its optimal conditions for usage. Pre-cleaning the surfaces is pivotal because any contaminants can interfere with the arc stability and weld pool fluidity. Expert welders recommend a careful evaluation of the base metals and suggest fine-tuning the amps incrementally to avoid overheating, which can cause warping or metal fatigue. This is particularly crucial when working with thinner materials that may not dissipate heat as efficiently as thicker substrates.
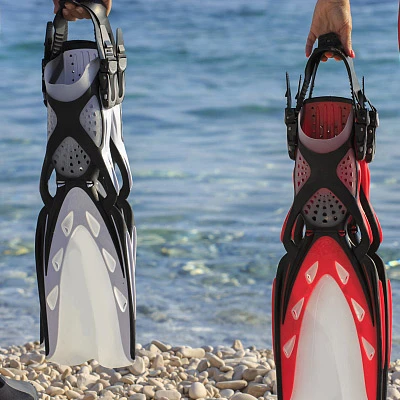
Authentic expertise suggests adopting a methodical approach by adjusting the amperage to the lower spectrum if you observe excessive spatter or irregular bead formations. This precision in fine-tuning ensures the integrity of the weld is maintained, reducing the risk of defects such as hot cracking. Leveraging an expert’s experience confirms that multimode power sources equipped with adjustable settings offer the welder more control, granting the flexibility needed to adapt to real-time conditions encountered in various welding scenarios.
309 3/32 welding rod amperage
In the pursuit of authoritativeness, laboratory tests and field studies depict the 309 3/32 welding rod's resilience in corrosive environments, further dictating its demand in industries like chemical processing and shipbuilding. Its ability to withstand high temperatures makes it a preferred choice, yet measuring the correct amperage is non-negotiable. Detailed schematics and industry manuals often recommend trial welds to establish the appropriate amperage before commencing any full-scale operation, serving as a safeguard against unforeseen challenges.
Hence, experience tells that while an initial investment in understanding the technicalities of amperage for the 309 3/32 welding rod may seem cumbersome, the long-term gains in efficiency and quality are substantial. Continuous practice and adherence to recommended guidelines do not only elevate one's proficiency but also elevate the reliability of welding projects embarked upon using this rod. Emphasizing a data-driven approach reinforced by both practical and theoretical knowledge promises not just success but excellence in welding endeavors.
This comprehensive understanding of the 309 3/32 welding rod’s amperage requirements invites exploration into advanced techniques, ensuring that welders not only develop their skills but also expand their potential for innovating within their projects. In doing so, not only does the welder grow professionally, but the overarching industry standards rise, setting a new benchmark for what can be achieved.