Choosing the right welding rod is a critical decision that influences the success and durability of any welding project. When it comes to 304 welding rods, professionals and hobbyists alike require a welding material that combines reliability with high-quality outcomes. The 304 welding rod stands out because of its compatibility with stainless steel applications and its impressive mechanical properties. Here, we delve into what makes the 304 welding rod an indispensable tool for both beginners and seasoned welders.
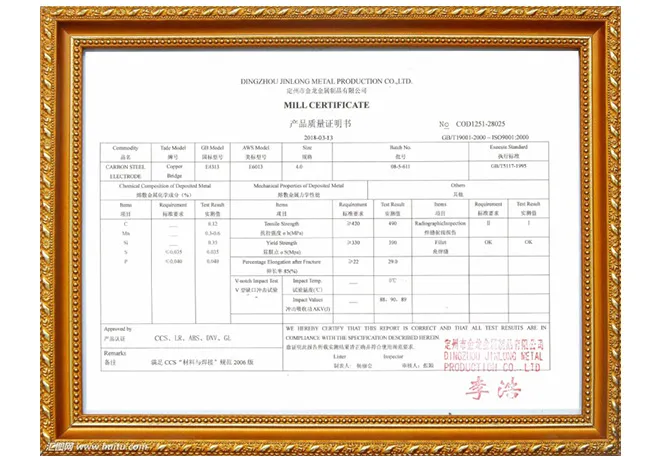
Experience reveals that 304 welding rods are uniquely suited for joining stainless steel components which require superior corrosion resistance. This makes them ideal for projects that need to withstand aggressive environments. Welders attest to 304 rods creating cleaner, more visually appealing welds, exhibiting fewer tendencies to produce slag inclusions, which is critical for maintaining the aesthetic and structural integrity of finished workpieces.
Examining the technical specifications, 304 welding rods possess a balanced chromium-nickel composition, which contributes to their exceptional rust resistance and formability. The inclusion of nickel enhances pliability while chromium counters oxidation, a vital factor for maintaining material strength in harsh environments. Experts therefore recommend 304 welding rods for constructing equipment exposed to saline conditions, such as marine, coastal, or outdoor structures where longevity is paramount.
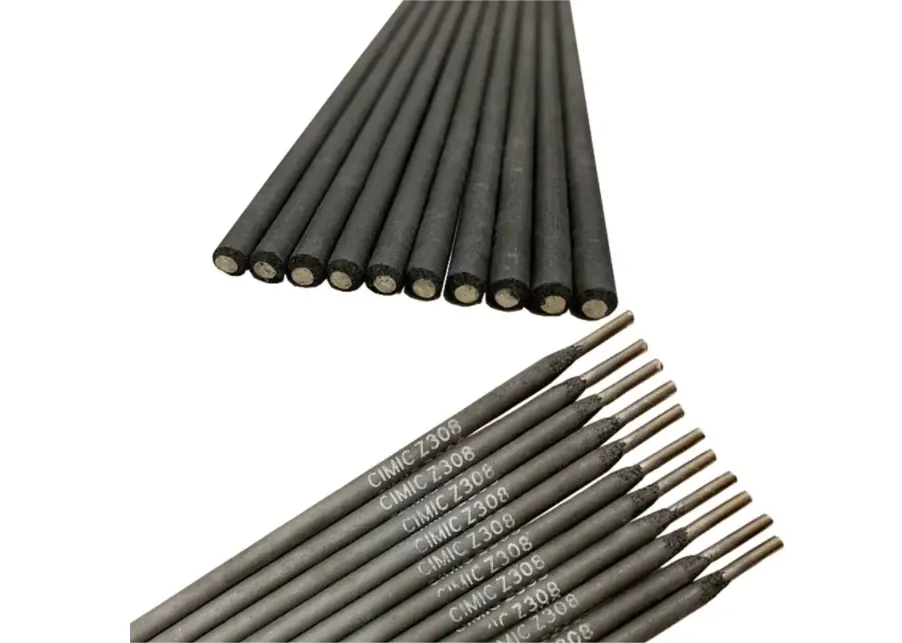
From an expertise standpoint, the choice of a 304 welding rod aligns with the demands for consistent performance in TIG and MIG welding processes. Professional welders praise the rod for its stable arc and smooth flow characteristics that contribute to reduced spatter and seamless penetration. For achieving the best results, pre-cleaning the base metal is advised to remove any contaminants, optimizing the interaction between the rod and the workpiece, thus ensuring a defect-free finish.
304 welding rod
Furthermore, the rod's versatility extends beyond maritime applications. It is favored in various industrial sectors including automotive, food processing, and chemical industries, where non-reactivity and hygiene are essential. The 304 welding rod's ability to retain strength at elevated temperatures makes it suitable for fabricating heat exchangers and exhaust manifolds, where thermal endurance and safety are non-negotiable.
Trustworthiness in 304 welding rods is affirmed by conformance to specific standards such as the AWS A5.9, which governs the chemical composition and mechanical attributes required for stainless steel welding fillers. Utilizing rods that meet or exceed these standards assures welders of achieving industry-grade quality that passes rigorous inspection criteria, making them a reliable component of structural frameworks that demand safety and durability.
The authoritativeness of 304 welding rods is continually reinforced by welding educators and industry publications, emphasizing the necessity for precision equipment and certified materials in welding practices. A comprehensive understanding of rod specifications, matched with proper equipment settings, significantly enhances the final output, ensuring projects not only succeed visually but also functionally.
In summary, selecting 304 welding rods confers multiple advantages across diverse applications, driven by their chemical resilience, mechanical stability, and adaptability to various operational conditions. Their reputable position in the market arises from empirical evidence and technical validation by welding communities and standards organizations. For serious welding professionals seeking reliability and excellence in stainless steel fabrication, the 304 welding rod remains a preferred choice, balancing expertise with practical application and trustworthy performance.