The choice of the right welding rod for metal thickness is a nuanced decision process, crucial to achieving a perfect weld, especially when dealing with various thicknesses. When selecting a 1/8 inch welding rod, proper understanding of its application, limitations, and benefits can significantly enhance your welding results and prolong the durability of welded structures. Building on extensive experience and industry expertise, here’s an in-depth guide to optimizing welding techniques with a 1/8 inch welding rod across different metal thicknesses.
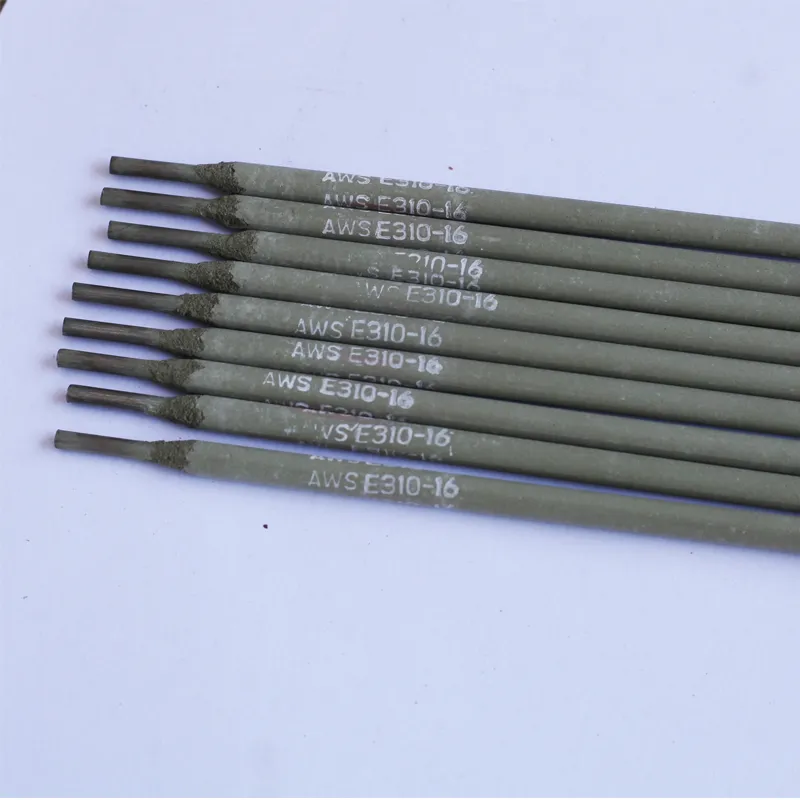
Experience shows that welding is as much an art as it is a science. The 1/8 inch welding rod stands out due to its adaptability in handling diverse metal thicknesses, which makes it a popular choice among welders.
This rod size is particularly effective in welding metal thicknesses ranging from medium to thick. Typically, it provides a good balance of penetration and deposition, ensuring that the weld pool is appropriately managed.
An essential aspect of utilizing the 1/8 inch rod effectively involves matching it with appropriate amperage. For thinner metals, setting your welder on the lower end of the rod’s amperage range (around 90-110 amps) minimizes burn-through risks while still ensuring a sound weld. Conversely, for thicker metals, the amperage should be increased (up to 150 amps), which promotes better penetration and fusion with thicker steel. Most experienced welders advise always performing a test weld on a scrap piece of the intended material to calibrate settings before committing to the actual weld.
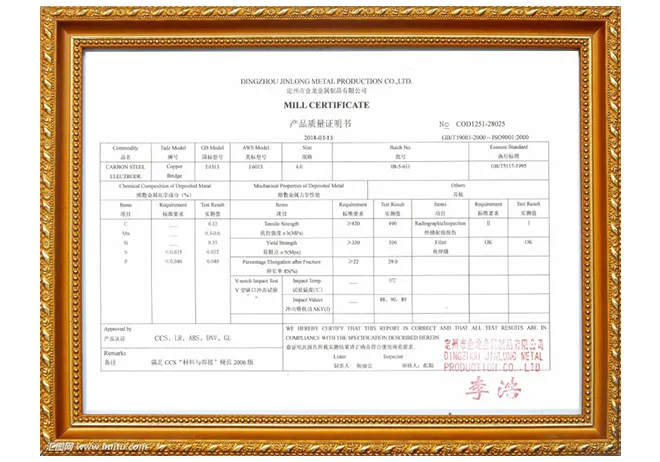
From an expertise perspective, the rod composition itself can influence performance. The 7018 rod, a common choice within the 1/8 inch category, is revered for its low hydrogen content, which reduces the risk of weld cracking. This makes it particularly beneficial when welding high-strength steel. However, the choice of electrode should always take into account both the chemical and mechanical properties of the base metal, the welding position, and whether AC or DC currents are used.
A crucial part of extending one’s expertise also involves understanding how different welding positions—flat, horizontal, vertical, or overhead—impact rod performance. The 1/8 inch rod offers remarkable versatility across these positions, but some may demand specific technique adaptations. For instance, vertical welding may require a weave or drag technique to control the molten pool, thereby preventing drips and ensuring consistent bead quality.
1 8 welding rod metal thickness
Authoritativeness in welding not only encompasses technical skill but also adhering to safety standards and best practices. This includes understanding the importance of rod storage and maintenance. For rods like the 7018, which are used extensively in structural welding, keeping them in a rod oven at recommended conditions (around 250°F) prevents moisture absorption, which could lead to hydrogen-induced cracking, compromising weld integrity.
With trustworthiness being a prime concern, particularly in structural applications, having certifications and standards compliance augments the credibility of your welding efforts. Following acceptable welding codes such as those from the American Welding Society (AWS) and ensuring that welds are inspected and tested (via methods such as ultrasonic or radiographic testing) can substantiate the reliability of welds made with 1/8 inch rods.
Product selection doesn't merely rest on empirical experience or isolated rides of trials, it also leverages technological advancements. For welding professionals venturing into automated welding processes, the choice of a 1/8 inch rod must consider compatibility with automated systems. Proficiency in configuring these systems to optimize rod performance outcomes is an invaluable asset, positioning you at the forefront of modern welding innovations.
In conclusion, mastering the use of a 1/8 inch welding rod involves a blend of experience, expertise, authoritative practice, and an unwavering commitment to quality and safety. Striking the balance between theory and practical application not only guarantees superior welds but also boosts productivity and craftsmanship in numerous sectors, from construction to automotive manufacturing. Navigate this complex yet rewarding terrain with informed decisions, and you will harness the full potential of your welding projects.