Selecting the right welding rod is crucial for both new and experienced welders. With an array of options available, choosing between specific rods, such as the 1/8” vs. 3/32” welding rods, becomes a vital decision in determining the success of a welding project. This article delves into the distinct features of these two popular welding rod sizes, offering insights into their applications, advantages, and considerations, thereby enhancing expertise and trustworthiness in choosing the right product.
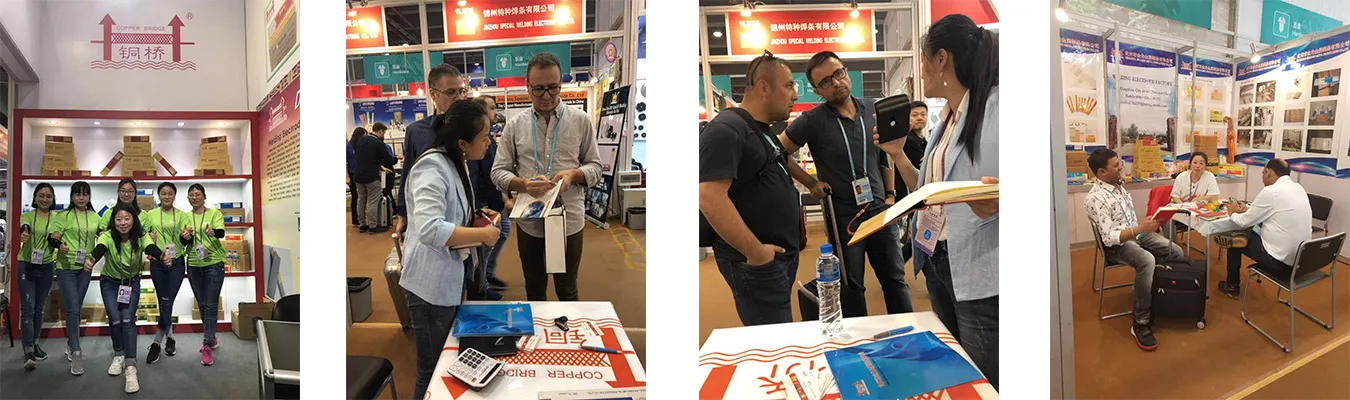
The 1/8” and 3/32” welding rods are both widely used for various types of welding projects due to their versatility and effectiveness. The primary difference between these rods lies in their diameter, which significantly affects their suitability for particular tasks.
1/8” Welding Rod
The 1/8” welding rod is thicker and often used for heavier applications. Its robustness makes it ideal for projects that involve thicker metal surfaces. This size offers several advantages
- Penetration Power The larger diameter allows for deeper penetration into the material, ensuring strong and durable welds, which is crucial for heavy-duty applications.
- Heat Tolerance This rod can handle higher amperage, making it suitable for projects that require significant heat application.
- Versatility It can be used on various metals including steel and iron, providing flexibility across different projects.
- Speed Due to its thickness, the 1/8” rod can facilitate quicker welds, thus reducing project time.
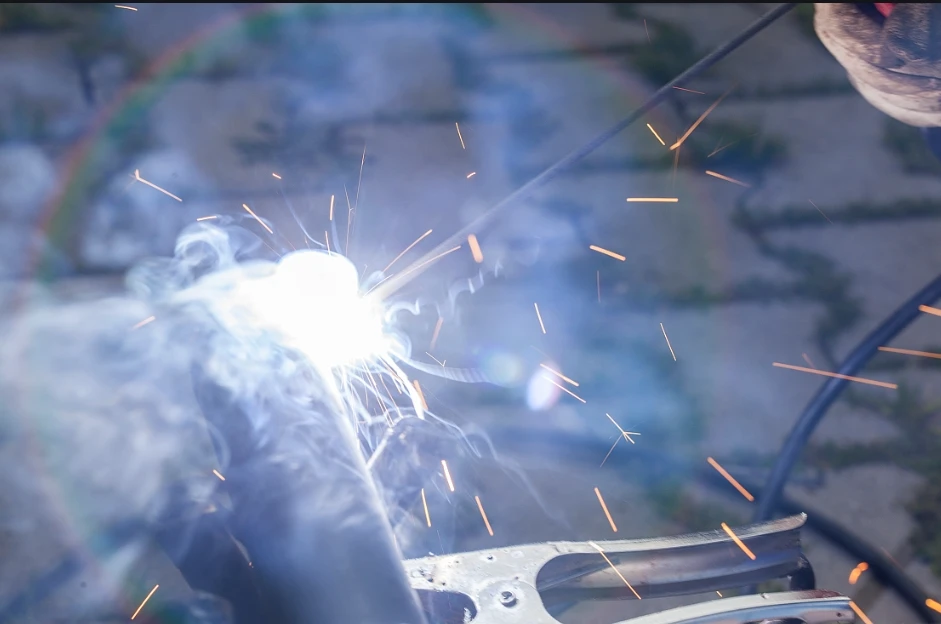
However, the 1/8” rod can be less precise than its thinner counterparts. It demands more skill to control and is less suited for thin materials, which could suffer from burn-through.
1 8 vs 3 32 welding rod
3/32” Welding Rod
Conversely, the 3/32” welding rod is thinner and often used for lighter applications and detailed work. Its size attributes to
- Precision It allows for more precise welding, making it ideal for intricate tasks where detail and finesse are critical.
- Lower Heat Requires less amperage, making it suitable for thinner metals, minimizing the risk of warping or burning through.
- Ease of Use Generally easier to manage for both beginners and experts when working on projects that demand control and attention to detail.
- Cleaner Welds Due to its precision and lower heat requirement, the 3/32” rod can yield cleaner welds with less splatter.
However, the 3/32” rod might not provide the same level of penetration and structural integrity needed for heavier materials, which can limit its application in industrial settings.
Selecting between these rods largely depends on the specific requirements of your project
- Material Thickness For welding thick materials, the 1/8” is preferable. For thinner materials or when dealing with precision parts, the 3/32” is more appropriate.
- Welding Position In vertical or overhead welding, the control offered by the 3/32” rod often makes it a better choice.
- Skill Level Beginners might find the 3/32” rod easier to work with due to its smaller size and reduced risk of overheating the workpiece.
- Project Type Consider the project’s needs; for structural work requiring robust joints, the 1/8” might be necessary. For art or automotive works where detail is vital, the 3/32” may be more advantageous.
In conclusion, understanding the characteristics and applications of 1/8” and 3/32” welding rods can significantly impact the success of your welding projects. The decision will largely hinge on material thickness, project requirements, and the welder’s expertise. By aligning these variables with the appropriate rod size, welders can ensure optimal performance and project outcomes. Developing a keen understanding of these tools reflects a commitment to expertise, authoritativeness, and trustworthiness in the field of welding.