Choosing the right welding rod is crucial for ensuring the quality and strength of a weld. Among the various options available, the distinction between a 1/8 inch welding rod and a 3/32 inch welding rod is significant, impacting both the performance of the weld and the ease of use for the welder.
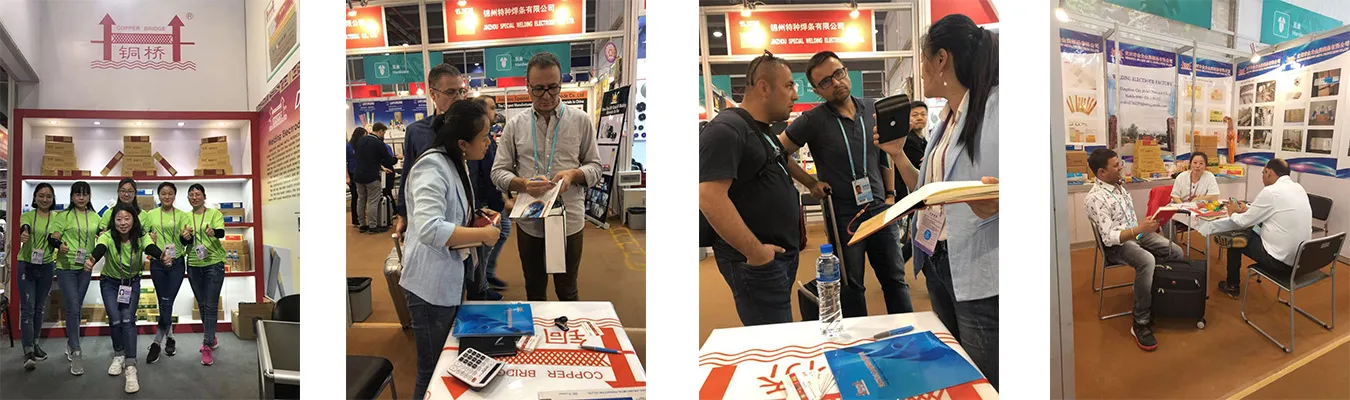
A seasoned welder understands that the size of the welding rod must be selected based on the material thickness, the type of welding process, and the position of the weld.
The 1/8 inch welding rod is typically employed for heavier metal gauges. This size allows for a higher deposition rate, which translates to faster welding speeds and more robust welds on thicker metals. This rod size is ideal for structural welding applications, where strength and integrity cannot be compromised.
Conversely, the 3/32 inch welding rod is commonly used for thinner materials or when precision is paramount. It is easier to maneuver and control, making it suitable for delicate or intricate welds, such as those needed in automotive repair or thin-wall tubing projects. The smaller size allows welders to work at a slower pace, accommodating detailed work without overheating or warping the metal.
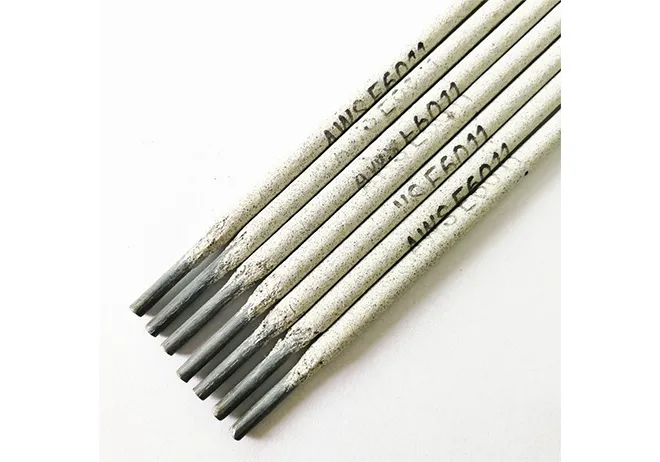
From an expertise standpoint, understanding the amperage requirements is essential. The 1/8 inch rod generally requires higher amperage, which means a more powerful welding machine is necessary. Conversely, the 3/32 inch rod operates efficiently at lower amperage, allowing it to be used with more compact, less powerful welding machines. This flexibility makes it a popular choice for hobbyists and professionals alike when working in settings with limited power supplies or on-site repairs.
1/8 vs 3/32 welding rod
Authoritative knowledge of welding materials also underscores the differences in flux types of these rods. The 1/8 inch rod often features a thicker flux coating, which provides deeper penetration and superior shielding against contaminants, ensuring the weld's integrity on thicker materials. Meanwhile, the 3/32 inch rod, with its thinner flux coating, offers a smoother finish and is less prone to spatter, a significant advantage when surface appearance is crucial.
The trustworthiness of a weld not only depends on the rod size but also on the welder's skill and the equipment's quality. In both cases, consistent inspection and maintenance of welding equipment are crucial to avoid potential failures. Welders should regularly check rod condition, as moisture can compromise their effectiveness, leading to poor weld quality.
A professional approach integrates these considerations with an awareness of productivity and cost efficiency. Larger rods like the 1/8 inch can minimize downtime due to fewer rod changes during welds on extensive projects, while the 3/32 inch offers cost savings when detailed, precision work negates the need for excessive material deposition and reduces post-weld clean-up time.
In conclusion, the choice between a 1/8 inch and a 3/32 inch welding rod hinges on the specific demands of the welding task at hand. Recognizing the strengths and limitations of each rod size allows both novices and experienced welders to enhance their work quality, efficiency, and safety, tapping into their individual advantages while mitigating potential drawbacks. Proper selection, combined with skillful application, ensures both the success and sustainability of welding projects across various industries.