Choosing the right welding rod is critical for successful welding projects, and understanding the specifics of rods such as 1/8 or 3/32 welding rods can significantly impact the quality and efficiency of your work. As an experienced welder and an expert in welding equipment, it’s essential to share insights that ensure authoritative and trustworthy guidance for those seeking to improve their welding skills and results.
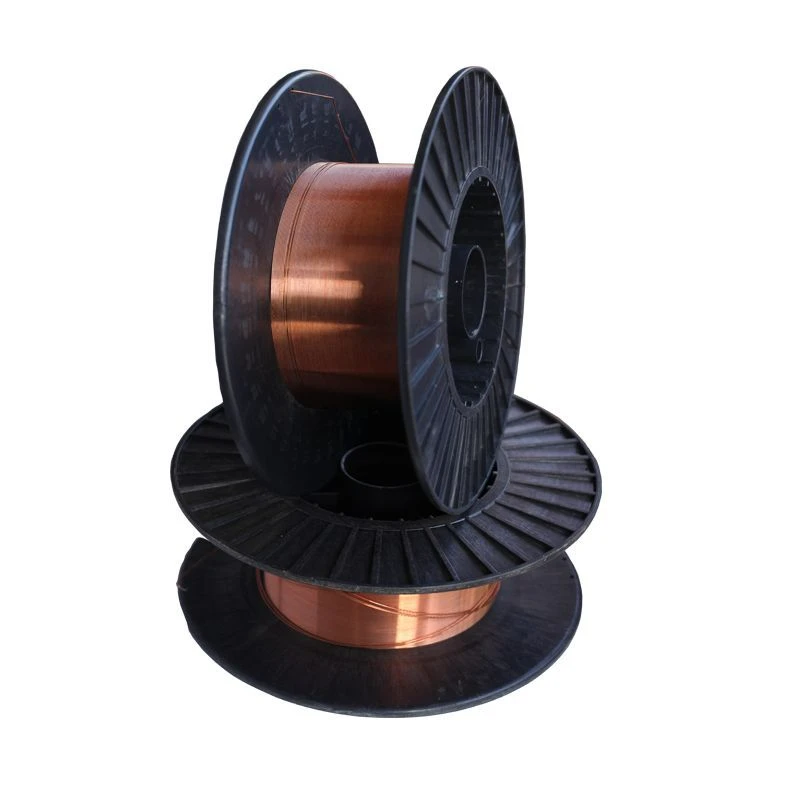
1/8 and 3/32 welding rods are pivotal tools within the welding community, each offering unique advantages depending on the specific project requirements. Welding rods, commonly referred to as filler metals, are used in arc welding to join two pieces of metal. They are available in various sizes and material compositions, but understanding the distinguishing features of 1/8 or 3/32 rods allows for precision in selection, ultimately affecting the strength and durability of the weld.
1/8-Inch Welding Rods The Sturdy Choice
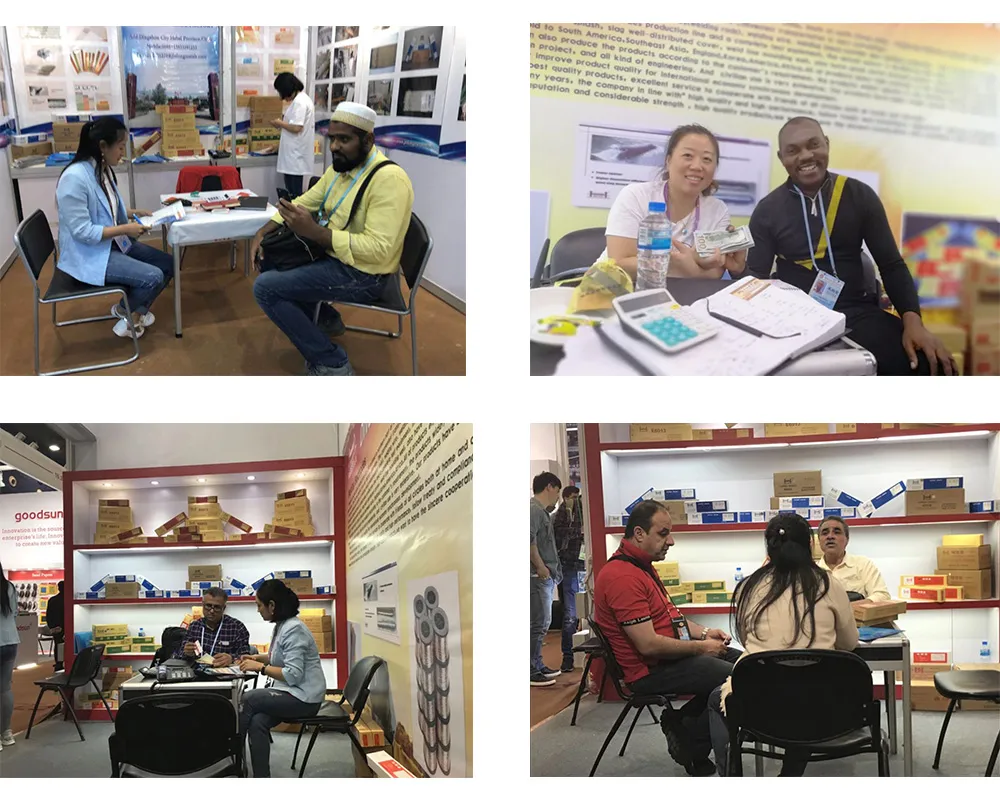
1/8-inch welding rods are known for their robustness and are often used in heavy-duty applications. Their larger diameter offers higher deposition rates, making them ideal for tasks requiring deeper penetration and faster welding speeds. This size is most commonly associated with projects involving thicker materials, typically 3/16-inch or thicker, such as structural steelwork or heavy machinery repair.
The increased diameter of the 1/8-inch rod ensures a stronger weld, providing more structural integrity to the finished product. Expert welders prefer this size when working with industrial-grade materials and situations that demand a reliable weld under significant stress. Additionally, experienced welders find that utilizing 1/8-inch rods can improve efficiency in larger projects as it reduces the number of passes required to complete a task.
Despite their benefits,
1/8-inch rods are not always suitable for delicate or intricate welding tasks. Their larger size can make it difficult to control heat and maintain a fine bead on thin materials. Hence, welders must assess their project requirements carefully before opting for this type of rod.
3/32-Inch Welding Rods Precision and Finesse
1/8 or 3/32 welding rod
In contrast, 3/32-inch welding rods are characterized by their ability to deliver precise welds with delicate control, making them particularly effective for thin or lighter materials, generally below 3/16-inch thickness. Their smaller diameter allows for tighter control over the bead and less heat input, reducing the risk of warping or burning through the substrate.
These rods are predominantly used in applications such as auto body repair, thin-sheet fabrication, and crafts that require fine detail work. They provide a more manageable flow, which is beneficial in achieving neat, aesthetically pleasing welds without sacrificing strength. For hobbyists and professionals alike, 3/32-inch rods offer versatility in different welding positions, including overhead and vertical-up, which require precise manipulation.
Expert welders appreciate the adaptability of 3/32-inch rods in various environments, recognizing them as ideal for creating quality welds on lightweight projects. However, when using these rods, it is critical that welders have a steady hand and an understanding of the appropriate amperage settings to prevent overheating the material.
Choosing Between 1/8 and 3/32-Inch Rods
The decision between using 1/8 or 3/32 welding rods ultimately hinges on the material thickness, the welding position, and the desired finish quality. Both options offer unique benefits, and the choice should be guided by careful consideration of the project’s technical requirements. An understanding of the welding environment, including factors such as power source (AC or DC), position, and necessary penetration depth, will also influence the decision.
Furthermore, it's essential for welders to have a comprehensive understanding of the electrical characteristics necessary to optimize the performance of their chosen rod. The welding current (amperage) settings required will differ significantly between the two diameters. 1/8-inch rods generally require higher amperage compared to their 3/32-inch counterparts to achieve proper penetration and maintain an even weld pool.
Ultimately, mastering the art of welding with 1/8 or 3/32 rods enhances a welder’s skill and project outcomes, leading to a more efficient, reliable, and quality-focused craftsmanship in their field. With experience and expertise, welders can effectively select and utilize the appropriate rod for each individual project, ensuring both the strength and aesthetic quality of their welds are uncompromised.