Understanding and optimizing the use of a 6013 welding rod is paramount for any professional welder or DIY enthusiast aiming for perfection in their craft.
The 6013 welding rod, known for its versatility, is a staple in workshops around the globe. However, to harness its full potential, understanding the role of amperage is crucial.
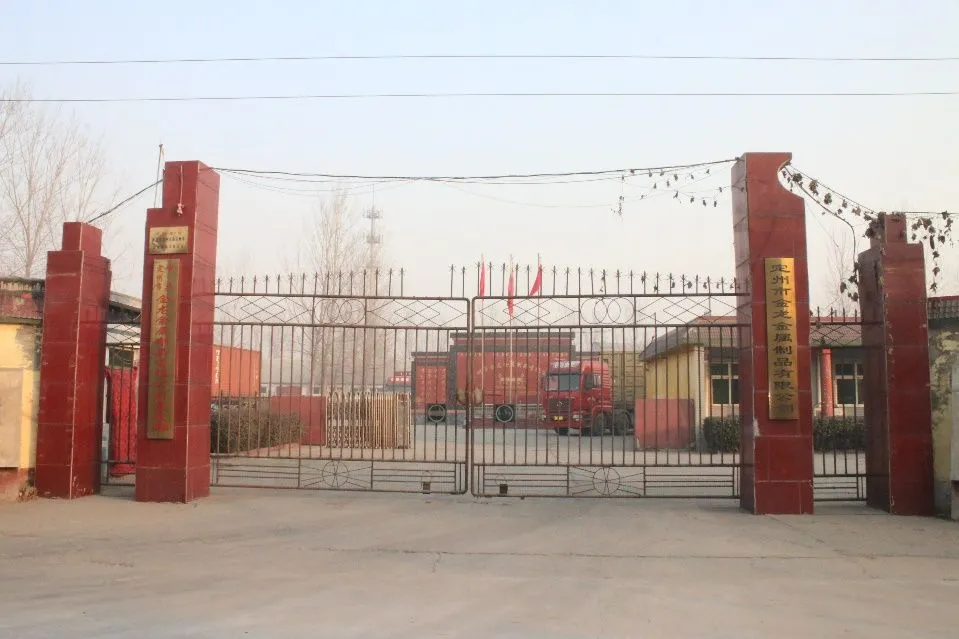
The 6013 rod is designed to work with both AC and DC currents, making it incredibly adaptable to different work environments and power supplies. The recommended amperage for a 6013 rod typically falls within the range of 40 to 180 amps, depending on the rod's diameter and the workpiece thickness. Understanding this range is critical to achieving optimal weld quality, avoiding defects, and ensuring safety.
For 1/8 inch (3.2 mm) 6013 rods, an amperage setting between 90 to 130 amps often provides the best results. This range supports moderate penetration and a smooth arc, suitable for welding thin to medium-thickness metals. It is particularly effective for positions such as flat, horizontal, and overhead welds, offering flexibility without compromising integrity.
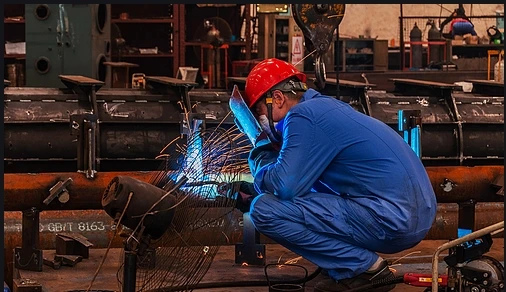
Experience reveals that using lower amperage settings can result in a softer arc. This can be beneficial when welding thin materials—such as sheet metal—to reduce the risk of burn-through. Conversely, higher amperage settings increase penetration and the speed of welding, which is advantageous when working with thicker materials where deeper fusion is necessary.
Expertise in handling a 6013 welding rod also involves understanding its unique characteristics. It produces a soft arc, smooth weld appearance, and easily removable slag, making it forgiving for those still developing their welding skills. The rutile coating of the 6013 creates a stable arc with good mechanical properties suitable for a wide range of applications, from metal fabrication to repair work.
1 8 6013 welding rod amps
Authoritativeness in this realm comes from acknowledging the collective input of welding professionals and industry standards. Many experienced practitioners have documented successes and failures with various amperage settings, contributing to a wealth of shared knowledge. Standards set by welding institutions and equipment manufacturers further guide optimal settings and use cases, ensuring consistency and reliability in practices.
Trustworthiness in welding comes from both personal practice and adherence to these established guidelines. Before starting a project, it’s critical to perform test welds, especially when working with new materials or projects, to ensure that the settings produce the desired quality of weld without introducing defects or compromising structural integrity.
Moreover, consulting equipment manuals and material specifications can offer additional insights into the appropriate amperage settings for specific tasks. Many manufacturers provide detailed charts and guidelines that correlate material thickness, rod diameter, and recommended amperage, making them invaluable resources.
In conclusion, mastering the appropriate amp settings for a 6013 welding rod enhances welding technique, ensuring robust and aesthetically pleasing welds. By devoting attention to experience, expertise, authority, and trustworthiness, both seasoned welders and newcomers can significantly improve their craft, delivering results that meet industry standards and withstand the test of time.