Choosing the right amperage for your 6010 welding rod is crucial for ensuring both the quality and safety of your welding projects. The 6010 welding rod, famous for its deep penetration and strong welds, is often used in applications where a high level of weld integrity is required. This includes projects such as structural welding, piping, and repair projects where access may be limited. Understanding the specific requirements and capabilities of the 6010 welding rod can significantly affect the outcome of your work.
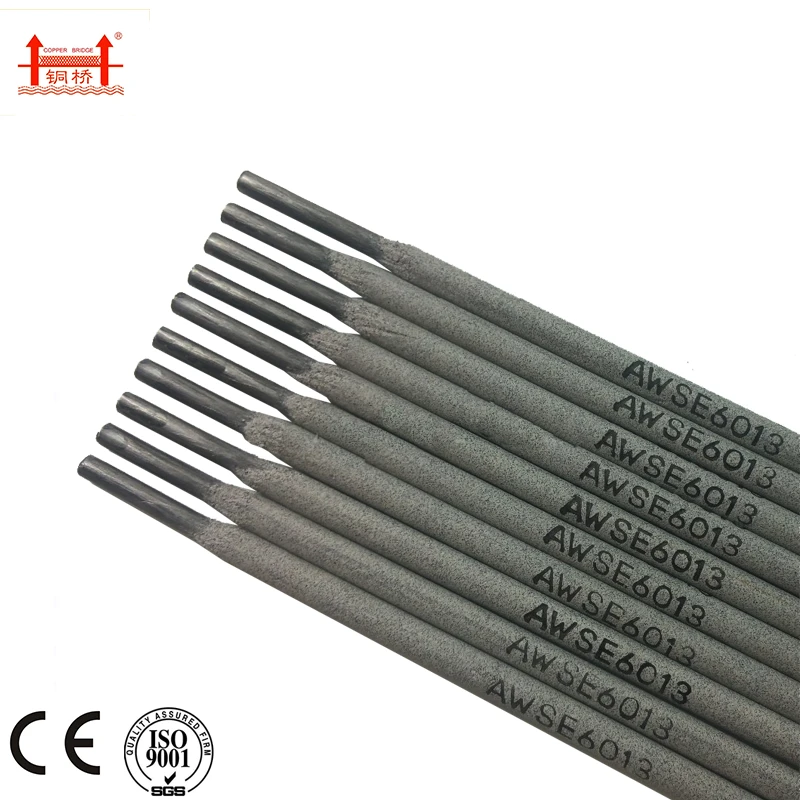
Amperage plays a pivotal role in the effectiveness of any welding rod. For the 6010 welding rod, typically a range of 75 to 125 amperes is recommended, though this can vary based on the specific diameter of the rod and the welding position. It's essential to match the amperage to the thickness of the material being welded and the ambient conditions in which you are working. For instance, thinner materials will require lower amperage to prevent burn-through, while thicker materials will need a higher setting to achieve proper penetration and fusion.
When setting amperage, one should consider the rod's diameter. A 1/8 inch 6010 welding rod works well between 75 to 125 amps, but this range can shift slightly based on user experience and specific project needs. The 6010 rods are designed for welding in all positions, which offers considerable flexibility, but demands mindful amperage adjustments as vertical and overhead positions often require a lower amperage setting to prevent excessive spatter and maintain control over the weld pool.
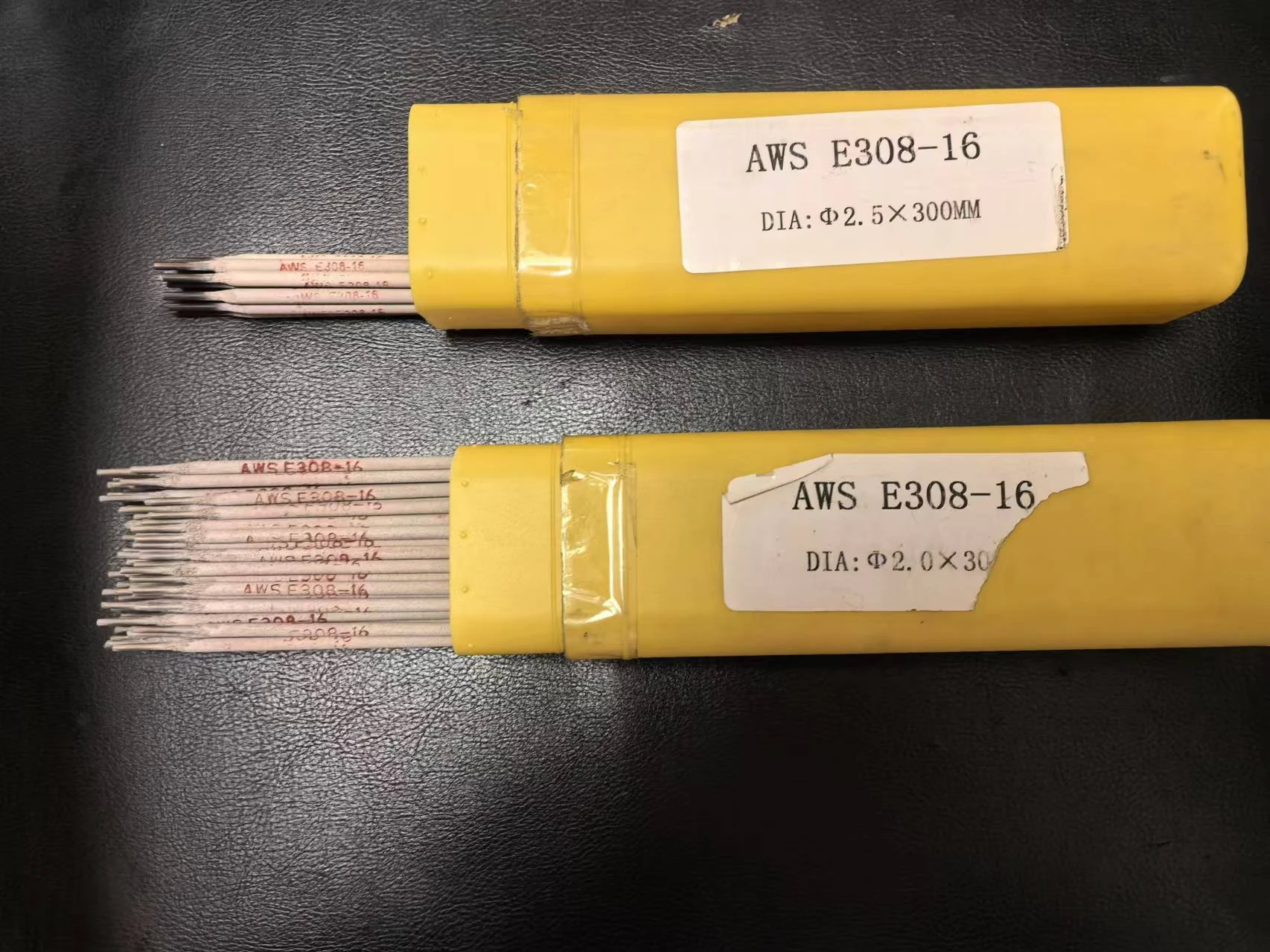
Another factor to consider is the power source. The 6010 rod operates optimally on DC (Direct Current) electrode positive (DCEP), which helps maintain a stable arc. Using a properly calibrated welding machine will also ensure consistent performance. It’s advisable to regularly check and maintain your welding equipment to uphold the safety standards and efficiency of the operation. A miscalibrated machine can lead to an incorrect amperage which not only affects weld quality but also compromises safety.
1 8 6010 welding rod amperage
Every material and environmental condition can influence your choice of amperage. A seasoned welder might adjust amperage based on the subtleties of the project at hand. For outdoor welding where the metal might be colder, a higher amperage setting can compensate for heat loss. Conversely, welding in a controlled indoor environment may allow for lower amperage settings as there are fewer variables to consider.
Furthermore, the amperage setting can affect the 6010 rod's performance in terms of penetration and cleanliness of the weld. Too low of an amperage may lead to inadequate penetration, resulting in a weak weld prone to failure. Conversely, an excessively high amperage might cause burn-through or warping, especially in thinner materials. The key is to achieve a balance where the arc is stable, the penetration is to the desired depth, and the weld bead is uniform without excessive spatter.
To master the use of the 6010 welding rod, one should consider ongoing practice coupled with an understanding of material properties and welding conditions. Additionally, engaging with other welding professionals through forums and workshops can provide invaluable insights and tips tailored to specific applications or uncommon scenarios you might encounter.
In conclusion, the 1/8 6010 welding rod, with its robust capabilities, demands a welder who is attentive to the nuances of amperage settings and the specific welding environment. Through careful calibration and practice, optimal results can be achieved with the 6010 rod, ensuring durable and high-quality welds. As with any technical skill, continuous learning and adaptation are crucial, making the mastery of welding both an art and a science.