Stainless steel TIG welding rods are an essential component for any welding project involving stainless steel. Among the various types of welding rods, the 1/16 stainless steel TIG welding rod stands out due to its specific characteristics that make it suitable for precise and delicate welding tasks.
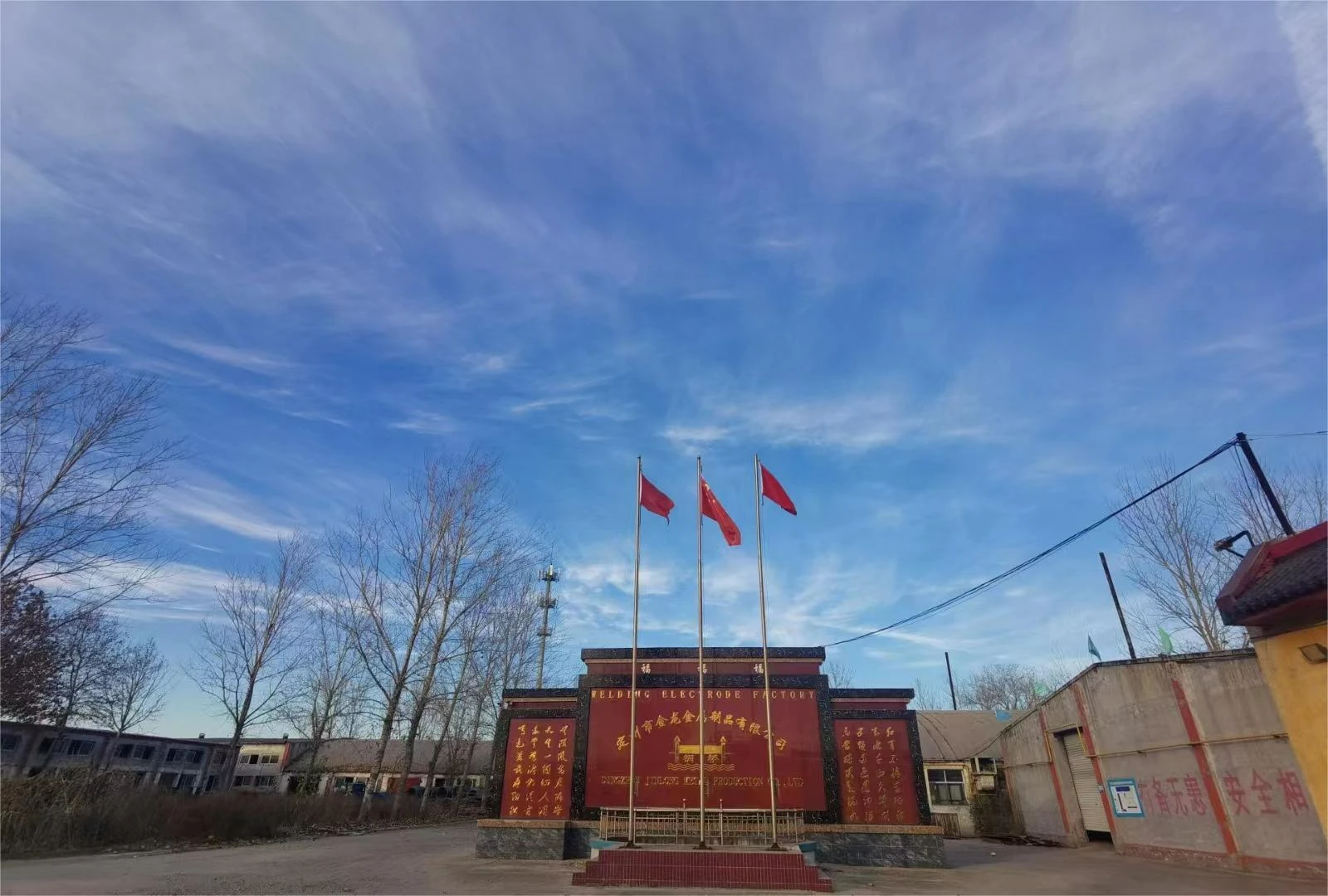
To understand why the 1/16 stainless steel TIG welding rod is favored by professionals, it's essential to delve into its properties and applications. Stainless steel, known for its corrosion resistance and strength, requires welding rods that can provide equally robust and durable welds. The 1/16-inch diameter of the rod indicates its suitability for tasks requiring fine control and precise welds, which is crucial when working on thin stainless steel materials or when intricate welding is necessary.
The composition of stainless steel welding rods is carefully engineered to enhance weld quality. Typically, these rods consist of alloys that include chromium, nickel, and molybdenum. Chromium enhances corrosion resistance, a critical factor for maintaining the integrity of stainless steel structures in harsh environments. Nickel contributes to strength and toughness, while molybdenum increases the overall resistance to pitting and crevice corrosion. These elements work synergistically to ensure high-quality welds that maintain the stainless steel's inherent properties.
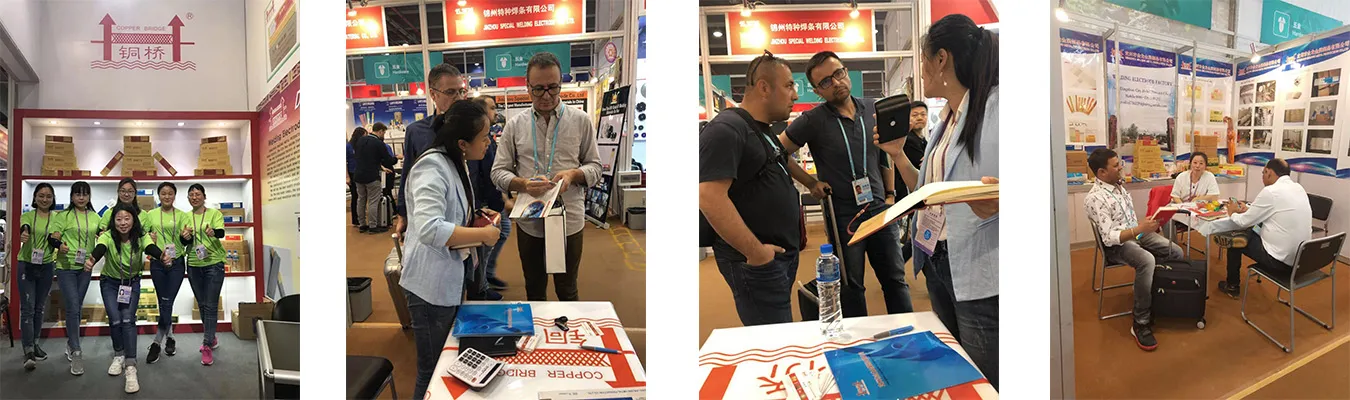
In practice, using a 1/16 TIG welding rod involves several technical considerations that underscore the need for expertise. TIG welding, short for Tungsten Inert Gas welding, employs a non-consumable tungsten electrode to produce the weld. The welder must maintain a steady hand and ensure the correct heat input to avoid warping or damaging the stainless steel, especially when dealing with thinner materials. The small diameter of the 1/16 rod allows for a narrow bead, providing intricate control over the weld pool. This precision makes it ideal for projects in the automotive industry, aerospace applications, and detailed metal art.
Expert welders often stress the importance of cleanliness and preparation in TIG welding. Stainless steel surfaces must be free of contaminants, oils, and rust to prevent defects and ensure a strong bond. Furthermore, the choice of shielding gas plays a crucial role in protecting the weld from oxidation. Argon is commonly used due to its inert properties, ensuring that the molten weld pool remains uncontaminated by atmospheric gases.
1 16 stainless steel tig welding rod
From an expert perspective, the 1/16 stainless steel TIG welding rod requires a precise balance between heat and technique. Welders must adjust their amperage settings according to the thickness of the material and the desired penetration depth. Too much heat can lead to burn-through, while insufficient heat may result in a weak joint. Therefore, mastering the art of TIG welding with these rods is a testament to a welder's skill and understanding of metallurgical principles.
Choosing the right 1/16 stainless steel TIG welding rod also involves understanding the specific grade of stainless steel being welded. Different grades, such as 304, 316, and 321, have unique properties and welding requirements. For instance, 316 grade, with higher molybdenum content, is used in marine environments due to its enhanced corrosion resistance. Selecting a compatible rod ensures that the weld will not only be strong but also maintain the specific characteristics of the stainless steel grade involved.
The trustworthiness of a weld is paramount in industries where safety and durability are non-negotiable. A well-executed TIG weld using a 1/16 stainless steel rod is virtually indistinguishable from the base material when done correctly, providing seamless joints that withstand mechanical stresses, chemical exposure, and thermal cycles. This reliability underscores the authority that skilled welders wield in ensuring the longevity and integrity of their work.
In conclusion, the 1/16 stainless steel TIG welding rod is more than just a consumable product; it is a tool that exemplifies precision engineering and skilled craftsmanship. Its application requires a fusion of technical knowledge, practical experience, and an unwavering commitment to quality. For both seasoned welders and novices seeking to enhance their skill set, understanding the nuances of using these rods can lead to improved weld quality and, ultimately, more successful projects. This expertise not only reinforces the authoritative nature of the welding profession but also cultivates trust among clients and peers alike.