Understanding 030 Solid MIG Wire Unveiling Excellence in Welding
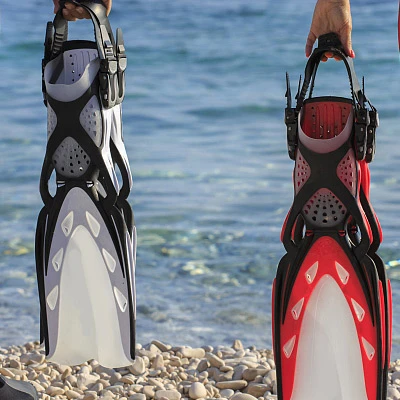
In the realm of modern manufacturing and construction, the significance of precision, efficiency, and reliability cannot be overstated. For industry professionals who rely on welding as a cornerstone of their craft, the choice of consumables becomes critical. Among these, 030 solid MIG wire stands out as an essential component, promising not only high performance but also exceptional versatility across various applications.
The Uniqueness of 030 Solid MIG Wire
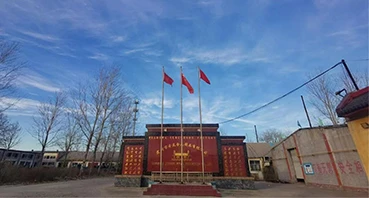
When discussing MIG (Metal Inert Gas) welding, the type of wire employed is pivotal to the welding process's outcome.
030 solid MIG wire is renowned for its balance in diameter, which offers a perfect mix between deposition rate and control during welding. This diameter size allows for enhanced maneuverability, making it particularly suited for welding thin materials where precision is key.
Professional welders often favor this wire for its ability to produce a stable arc with minimal spatter. This characteristic is invaluable, especially when working on surfaces where cleanliness and smoothness are essential. The production consistency of 030 solid MIG wires makes it a trusted partner for both seasoned professionals and hobbyists venturing into complex projects.
Superior Material Composition
Attention to the material composition of 030 solid MIG wire provides insights into its widespread acclaim. Typically crafted from high-quality steel alloys, the wire offers exceptional tensile strength, allowing for robust joint creation. This wire's metallurgical properties ensure not only strong welds but also those that are resilient to various forms of mechanical stress, enhancing the longevity and integrity of the welded structure.
Its uniform composition also means consistent performance, whether you're pulling a continuous bead or making intricate spot welds. Moreover, the wire's chemical makeup often includes elements like silicon and manganese, which enhance deoxidizing properties, consequently improving weld quality and reducing oxidation potential.
Practical Application Scenarios
The versatility of 030 solid MIG wire comes to the forefront when considering its applicability across multiple industries. Automotive manufacturing, for example, benefits from its capacity to create precise, aesthetically pleasing welds crucial for visible body parts. In construction, its strength supports the formation of durable frameworks and supports that require reliability over time. The field of metal art and sculpture also embraces this wire for its ease in crafting detailed metallic designs.
030 solid mig wire
Beyond industrial domains, this wire is also favored in DIY projects due to its adaptability in various settings and the ease of use with standard MIG welding machines.
Industry Expertise and Authority
Welding, much like any specialized trade, thrives on knowledge and the insights of experienced professionals. Veteran welders often emphasize the importance of choosing the right consumables; in this context, 030 solid MIG wire consistently earns their endorsement. With industry leaders and welding certification bodies often recommending this specification, it speaks volumes about its authority and reliability.
Moreover, manufacturers of this wire prioritize stringent quality control measures during production, backed by certifications and compliance with international welding standards. This ensures that every spool hitting the market meets the rigorous demands of professionals worldwide.
Building Trust Through Quality Assurance
030 solid MIG wire also enjoys a reputation for trustworthiness amongst users, primarily due to its track record of delivering on promises. Companies producing these wires often invest in exhaustive testing phases, ensuring products that can withstand diverse environmental conditions and rigorous operational challenges.
Furthermore, many manufacturers provide comprehensive technical support and resources, aiding welders in maximizing their product utility. This support ranges from detailed usage guides to responsive customer service, fostering a relationship where users feel confident in their equipment choices.
Conclusion
For those entrenched in the welding industry, or those looking to embark on their initial projects, the consideration of 030 solid MIG wire represents a decision grounded in performance, quality, and reliability. As a linchpin in achieving exemplary welding outcomes, this wire illustrates a nuanced balance of professional expertise and practical application.
The growing recognition of its advantages underscores the high regard users have for its consistency and strength. Ultimately, engaging with 030 solid MIG wire translates to embracing a standard of excellence in welding — a commitment to skill, precision, and enduring quality that transforms mere potential into realized accomplishment.