The world of welding is continuously evolving, driven by the demand for more efficient and durable fabrication solutions. In this sphere, the 030 MIG solid wire stands out as a critical component for both novice and professional welders who are keen on achieving precision and quality in their projects. The 030 MIG solid wire is not just a mere consumable; it's a vital tool for those who understand the art and science of welding.
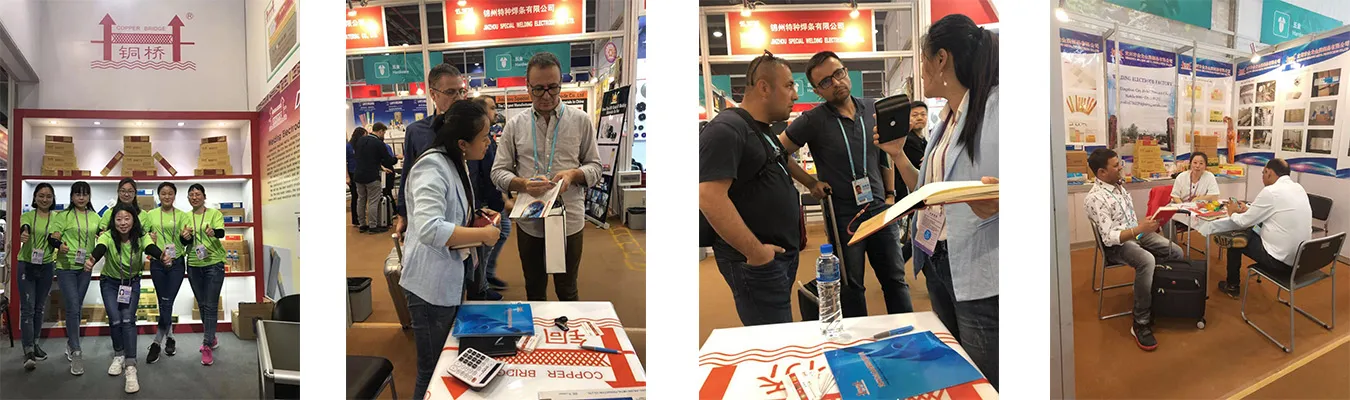
Understanding the 030 MIG Solid Wire A Deep Dive
First and foremost, the 030 designation refers to the wire's diameter, which is 0.
030 inches. This specific size is versatile, providing an excellent balance between thickness and flexibility. One of the main advantages of utilizing the 030 MIG solid wire is its ability to seamlessly weld thinner metal sheets, which is a necessity for automotive work, light-manufacturing tasks, and home repairs.
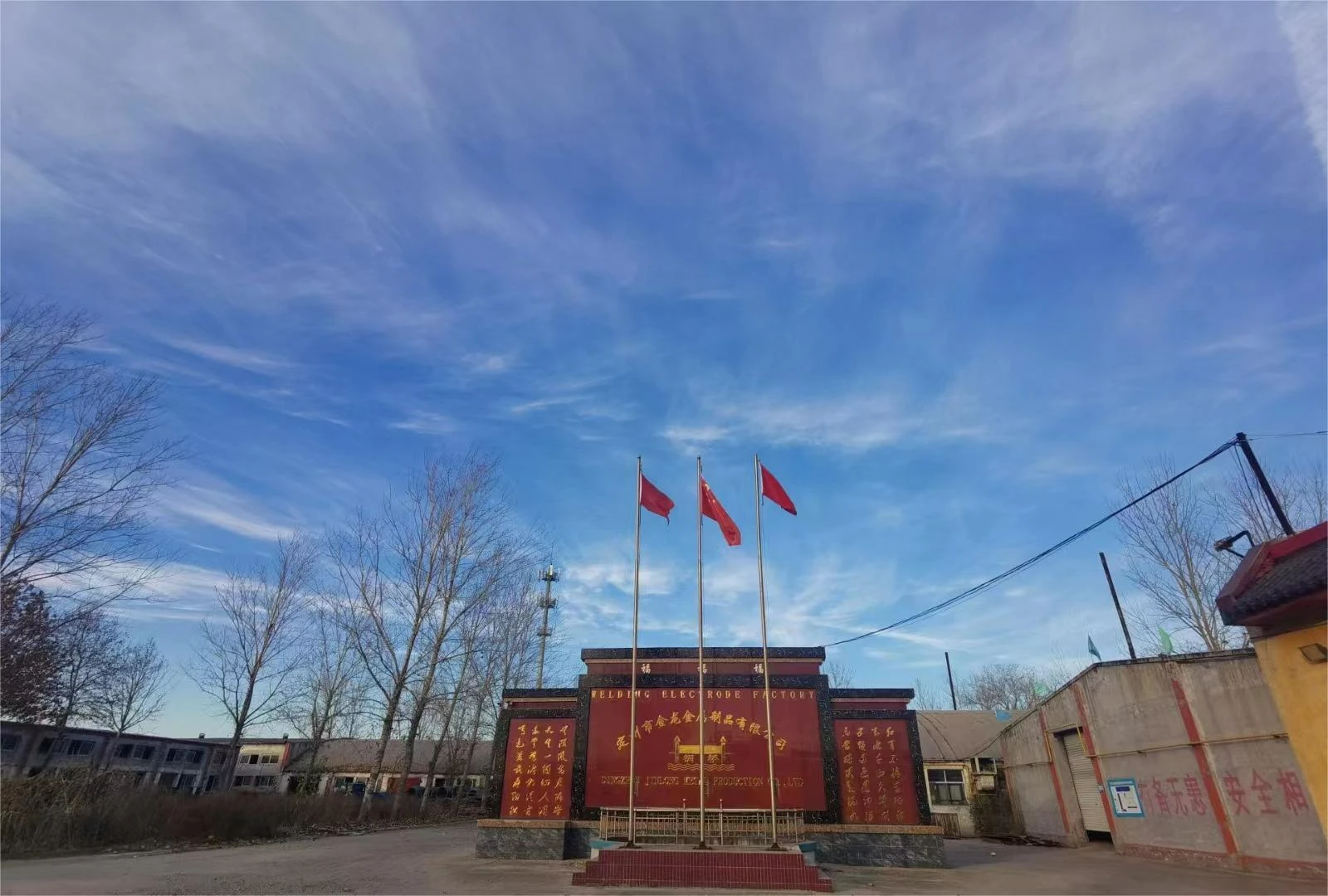
The composition and quality of the MIG solid wire cannot be overstated. Typically crafted from mild steel and mixed with deoxidizers like manganese and silicon, the 030 wire ensures minimal spatter and reduced cleanup time. This chemical make-up is crucial in producing clean welds, enhancing the structural integrity of the finished piece, and lowering the occurrence of porosity and inclusions—common flaws that can undermine weld quality.
Real-World Experience What Users Are Saying
For both hobbyists and seasoned professionals, experiences with 030 MIG solid wire highlight its advantages. Users often praise its smooth feed rate and consistency, essential qualities that facilitate steady welding arcs and reduce the likelihood of burn-through. Moreover, this wire type is compatible with a variety of shielding gases, such as a mix of Argon and CO2, which enhance its versatility across different welding environments.
Expertise in Application Achieving Optimal Results
To maximize the efficacy of the 030 MIG solid wire, a foundational understanding of MIG welding settings is required. Experts recommend setting the amperage and voltage based on the material thickness and the specific welding position. For instance, applying a higher voltage and wire feed speed is advisable when working with thicker metals, ensuring deeper penetration and stronger welds. Additionally, maintaining the correct gun angle—ideally between 15 to 20 degrees—can prevent defects and ensure a uniform bead.
030 mig solid wire
The expertise lies in adjusting these parameters to complement the specific features of the 030 wire. Operators should be adept at distinguishing between various joint types, making appropriate adjustments to achieve the desired weld contour and strength.
Authoritativeness Through Innovation
Manufacturers continue to innovate with 030 MIG solid wires, offering features like improved surface coatings that enhance feedability and reduce friction within wire liners. These advancements underscore the wire's reliability in high-demand applications, such as structural and fabrication industries.
Training programs and certification courses also increasingly focus on proper wire handling techniques, emphasizing the importance of maintaining ambient conditions that reduce moisture and contamination, further extending the wire's shelf life and performance.
Building Trust and Reliability
Trustworthiness in using 030 MIG solid wire stems from rigorous quality control processes employed during production. Reputable manufacturers adhere to industry standards, such as AWS (American Welding Society) requirements, ensuring each spool meets consistent performance benchmarks. This focus on standards assures welders of the wire's reliability and effectiveness, mitigating the risk of material failure.
Furthermore, consumer reviews continually cite the wire's adaptability and cost-effectiveness, with many users affirming its value for small-scale production runs and complex repair work. Its compatibility with a wide range of welding machines also positions it as a reliable solution for those seeking to enhance their operational efficiency.
In essence, the 030 MIG solid wire represents a critical intersection of technology, skill, and reliability in welding. For those in pursuit of precision and excellence, understanding the nuances of this wire type can significantly impact the quality of their work, establishing a foundation for continued success in various welding applications.