When selecting welding rods for specific tasks, understanding the nuances between different types is vital for optimal results.
Among the most discussed are the 6011 and 7018 welding rods. Both serve distinctive purposes in the welding industry and excel under various conditions. This article provides a complete comparison to assist you in selecting the suitable rod for your welding needs.
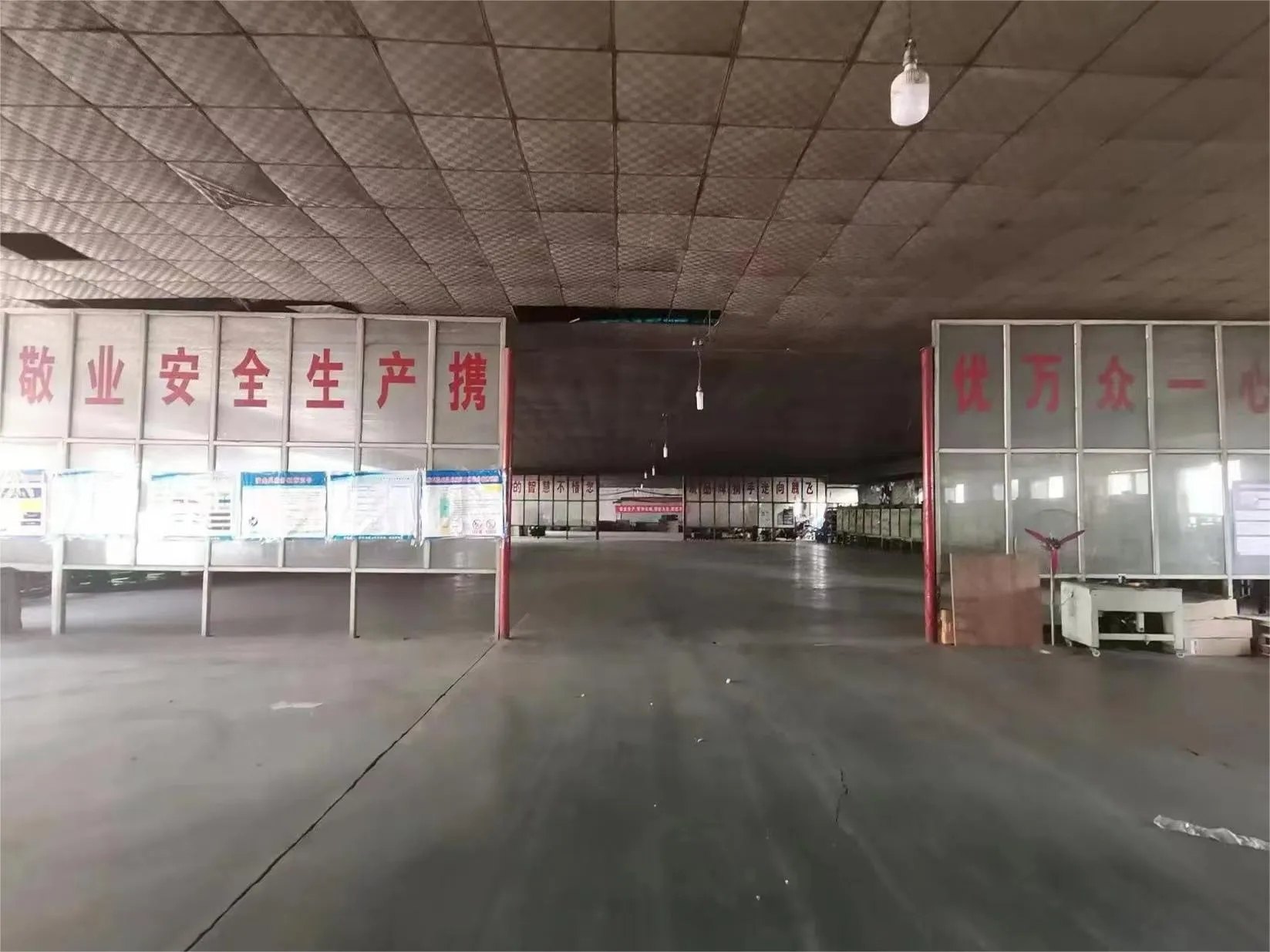
The 6011 welding rod is renowned for its versatility and all-position usability. It features a cellulosic flux coating, which allows it to penetrate rust, paint, and dirt. Hence, it is ideal for scenarios where thorough cleaning of the base metal is not feasible. The quick-freezing slag produced by the 6011 rod makes it exceptionally useful for vertical-up and overhead welding positions. Welders appreciate its effectiveness in maintenance and repair work, including farm equipment, pipes, and structural welding.
For beginners, the 6011 rod is relatively forgiving, requiring less precise manipulation than other types. However, its greatest merit lies in its deep penetration, which ensures strong welds even in less-than-ideal conditions. This depth of penetration makes the 6011 rod the go-to choice for emergency repair work and fieldwork where the materials involved are often in poor condition. However, its appearance post-welding sometimes lacks the smooth finish achievable with other rods, a factor to consider if aesthetics are crucial to the project.
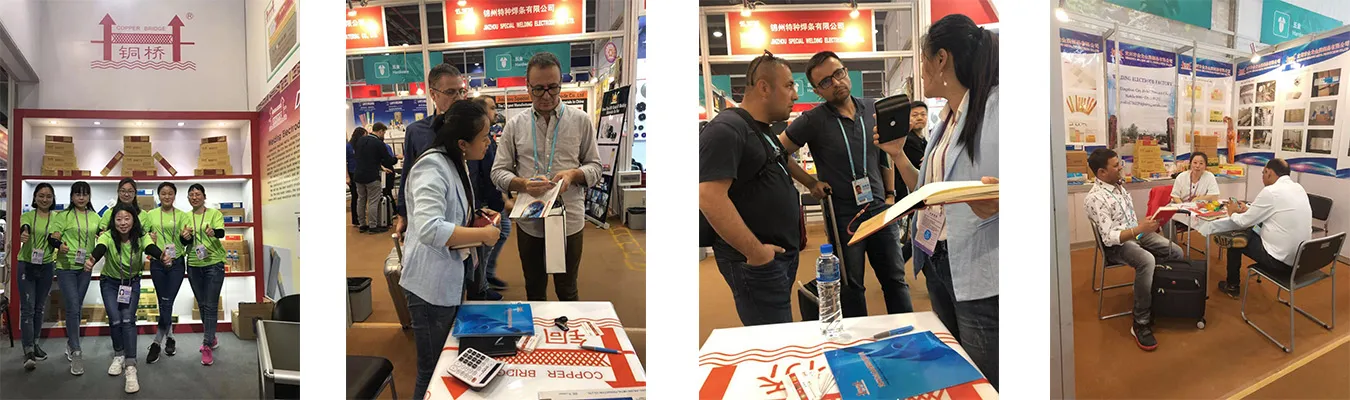
Switching focus to the 7018 welding rod, this type is distinguished by its low-hydrogen iron powder flux, offering a significantly smoother arc. It is especially favored for its ability to create strong, crack-resistant welds. The 7018 rod delivers a cleaner, more polished finish, making it a preferred choice for structural steel welding where appearance and integrity are paramount. Numerous industries, including construction and heavy equipment manufacturing, heavily rely on the 7018 for non-porous, aesthetically pleasing joints.
The 7018 rod requires a DC power source, although it can be used with AC under the right conditions. One notable consideration with the 7018 rod is its sensitivity to moisture. Proper storage is essential to maintain its low-hydrogen properties; exposure to humidity can lead to hydrogen-induced cracking in welds. This consideration makes it less desirable for fieldwork compared to the 6011, which thrives in less controlled environments.
While both rods have their unique strengths, they cater to different welding environments and objectives. The 6011 is adept at delivering strong welds on impure metals and is a favorite for on-the-spot repairs where cleanliness is not assured. In contrast, the 7018 excels in creating cleaner welds on prepared surfaces where reliability and aesthetic quality are crucial.
difference between 6011 and 7018 welding rods
A skilled welder often employs both types depending on the task. A project demanding robust structural integrity and precision will benefit from the 7018, while quick field repairs or work on less than pristine surfaces will see better results with the 6011. Ultimately, the choice between 6011 and 7018 rods depends on the welder's need for penetration vs. clean finish and structural soundness versus rapid and versatile application.
Expert welders also emphasize the importance of understanding the mechanical properties of these rods. The tensile strength of the deposited weld metal is another critical factor. The 6011 rod offers a tensile strength of approximately 60,000 psi, which is adequate for standard applications but may not meet the demands of higher-strength projects. Meanwhile, the 7018 rod surpasses this with a tensile strength of about 70,000 psi, catering to high-stress and load-bearing structures.
From an expertise standpoint, maintaining clean and proper techniques when using these rods is essential for achieving the best results. While the 6011 rod may forgive some deviation in technique, the 7018 demands precise control to ensure its low-hydrogen benefits are fully realized. Furthermore, adhering strictly to suitable storage conditions for the 7018 will prevent weld failures due to hydrogen entrapment.
In practice, welders should carry both rods to their job sites, ensuring they are equipped to handle a variety of welding tasks. Mixing the two based on the requirements of specific sections of a project can leverage the strengths of each rod, providing an optimal blend of mechanical strength and visual quality.
In conclusion, understanding the strengths and limitations of 6011 and 7018 welding rods enables welders to apply them effectively to their respective use cases. Skillful utilization of both rods, accompanied by adherence to best practices in storage and technique, guarantees superior weld quality, aligning with the expansive needs of the welding industry.