Choosing the right amperage for a 6010 welding rod, particularly in a 3/32 inch size, is crucial for achieving high-quality welds that are both strong and reliable. The 6010 welding rod is known for its deep penetration and is often used in situations that require welding through rust, oil, or dirt. It is a versatile choice for many professionals in the welding industry.
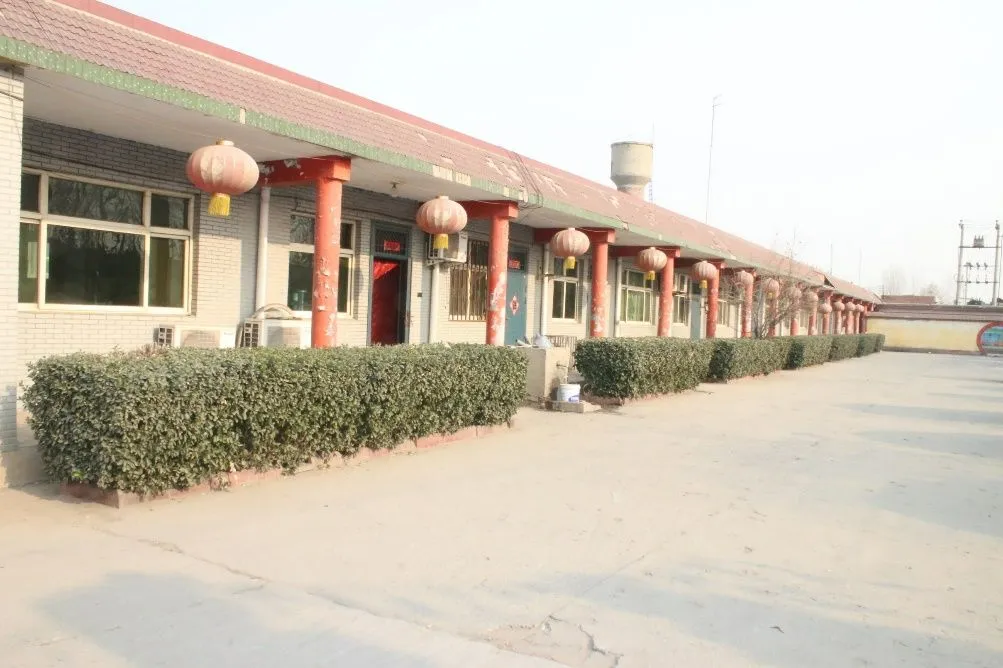
When working with a 3/32 inch 6010 welding rod, the ideal amperage range is typically between 40 to 80 amps. However, it's important to consider several factors that can influence the exact amperage setting necessary for any given project. These factors include the metal thickness, welding position, and specific requirements of the job.
For thinner materials, starting at the lower end of the amperage scale is advisable. This helps prevent burn-through, a common issue when working with thin metals. On the other hand, thicker materials may require higher amperage settings to ensure proper penetration and fusion of the weld. The increased amperage aids in maintaining a stable arc length, which in turn contributes to a more consistent and stronger weld.
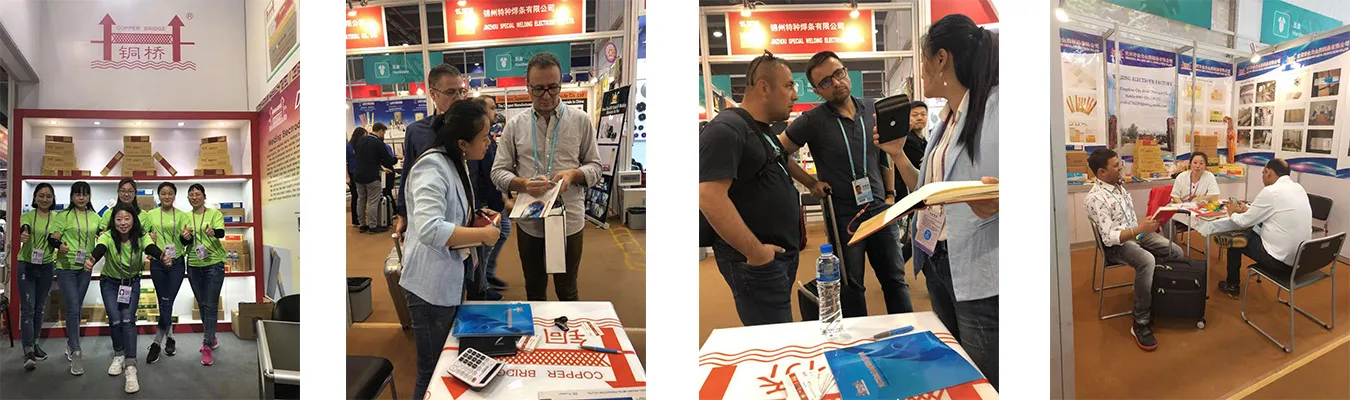
The welding position also plays a significant role in determining the appropriate amperage. For example, overhead welding can benefit from a slightly lower amperage to reduce the risk of molten metal dripping from the weld pool. Conversely, flat or horizontal positions might require higher amperage for optimal results. Adjusting the amperage based on the position not only increases safety but also improves control over the weld.
Moreover, material type can affect amperage settings. Mild steel, which is commonly used with 6010 rods, generally adheres to the standard amperage recommendations. However, for different alloys or metals with varying properties, adjustments may be necessary to accommodate differences in heat conductivity and melting points.
6010 welding rod amperage 3 32
Experience and skill level of the welder are also critical in finding the right amperage setting. Seasoned welders with a keen sense of their equipment can often make minor tweaks to amperage based on their intuition and past experiences, which comes from extensive practice and practical knowledge. For those less experienced, consulting equipment manuals or seeking advice from more experienced welders can be invaluable. This is where welding expertise transforms into authoritativeness, providing guidance grounded in real-world practice.
It is important to emphasize the role of testing and adjustments. Before committing to a final amperage setting for a significant project, conducting test welds is recommended. This practice not only verifies that the chosen settings are effective but also builds confidence in executing the task at hand. Trustworthiness in a welder’s choice of settings arises from consistent results that meet safety standards and project requirements.
Furthermore, maintaining equipment properly also impacts the amperage setting's reliability. Regular checks and timely maintenance ensure the welding machine operates within its intended parameters, delivering accurate amperage outputs. This adds a layer of confidence in the amperage settings and enhances the overall trust in the welding process.
In conclusion, the optimal amperage for a 6010 welding rod of 3/32 inch size may vary depending on specific project needs. A nuanced understanding of material characteristics, welding positions, and equipment efficiency, combined with professional experience, enhances weld quality. Remember, successful welding is a blend of scientific principles and hands-on expertise, demonstrating professionalism and credibility in the field.