Welding rods, an essential component of the welding process, come in various sizes and each size is tailored for specific applications. Choosing the appropriate welding rod size can be the difference between achieving a durable weld and a weak joint prone to failures.
Understanding welding rod sizes and their uses is fundamental for both seasoned professionals and hobbyist welders.
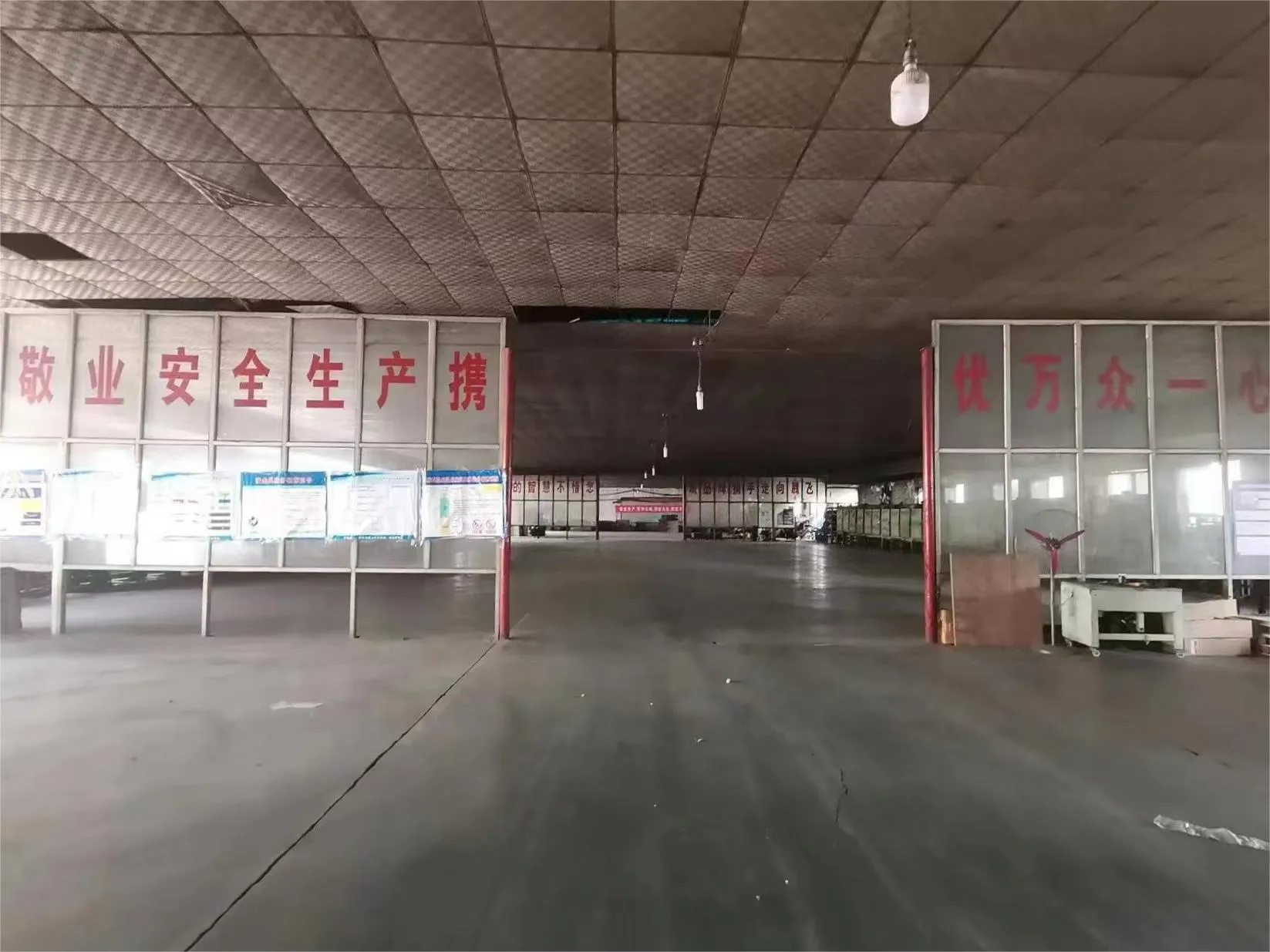
When discussing welding rods, it is crucial to focus on some key types predominantly used across various industries
1. 1/16-inch Rods These are ideal for small-scale projects and are best suited for welding thin metals. Due to their size, they require lower amperage, making them perfect for fine work, such as automotive repairs and general metal fabrication. Their smaller arc results in less heat and minimal risk of burning through thin gauge metals.
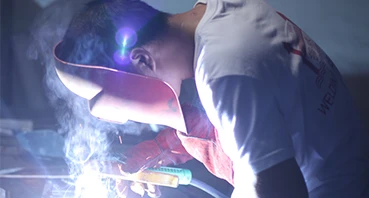
2. 3/32-inch Rods Slightly thicker, these rods are a versatile choice for medium-thickness materials. They are often used in residential and commercial settings for metal structures like railings, gates, and general maintenance repairs. With an adequate balance between penetration and deposition, they provide a stable arc and smooth welds, suitable for structural integrity.
3. 1/8-inch Rods Widely favored in the welding community, these rods provide the ideal balance of efficiency and penetration power. They're often used for welding heavy-duty materials such as steel beams and are capable of achieving deep penetration, facilitating the welding of thicker materials in construction and industrial applications.
4. 5/32-inch Rods Recognized for their robustness, they are frequently used in heavy industrial settings. These rods can handle more amperage, making them suitable for welding thick metal plates and heavy machinery. While they require more skill, their capacity to create strong bonds is unparalleled.
5. 3/16-inch Rods Primarily used for heavy construction and industrial applications, these rods demand high amperage and are not suitable for novice welders. They are designed for welding thick sections of metal and are popular in industries such as shipbuilding and pipeline construction.
welding rod sizes and uses pdf
Furthermore, even within these sizes, the choice of material is just as significant. Common types of rods include
- Mild Steel Rods Best for general-purpose welding, widely used due to their ease of use and compatibility with a wide range of metals.
- Stainless Steel Rods Necessary for projects requiring corrosion-resistant joints. They are critical in industries like food processing, where hygiene and durability are paramount.
- Aluminum Rods These must be used with care, as aluminum requires specific techniques for effective welding. They are favored in the aerospace and automotive industries due to their lightweight nature coupled with sufficient strength.
A nuanced understanding of welding rod sizes and the materials they are meant for can augment a welder's ability to tackle a variety of projects with confidence and precision. Such expertise not only improves efficiency but also ensures safety and quality compliance, fortifying the trust clients place in a welder's skillset.
Building credibility as a welding expert involves hands-on experience across different projects and continuous education in evolving welding technologies. Trustworthiness derives not just from technical skill but also from adherence to best practices and industry standards, ensuring all welds meet regulatory requirements.
In conclusion, the optimal choice of welding rod size and type depends on the specific demands of the project and the materials involved. Through experience and understanding, a welder gains the ability to select the right tool for each unique application, displaying not only expertise in welding but also a commitment to quality and safety.